3D Printer for Industrial R&D
The Research and development industry is a very crucial part of many industries that need to keep up with trends and competitive demands.
We provide highly efficient 3D printers for industrial research and development. This technology industry is an essential contributor to the research and development industry.
How 3D printers work for Industrial R&D
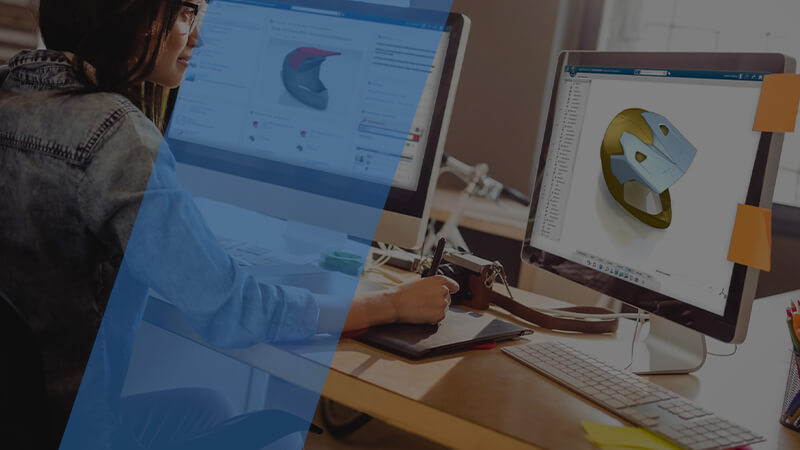
3D design
Components
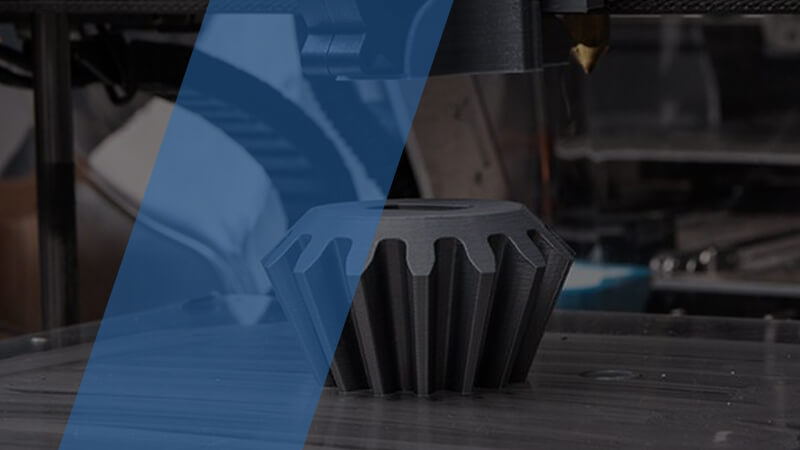
3D printing
Components
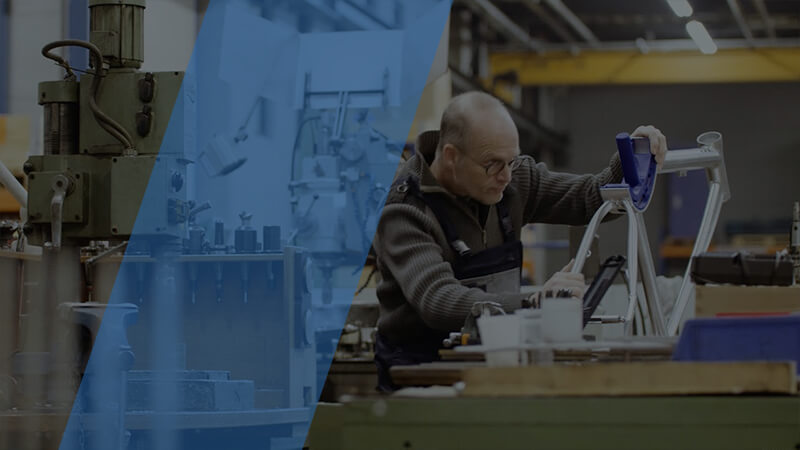
Processing
Components
The 3D printer is the process of making 3 dimensional solid objects from a digital file. The creation of the 3D printed object is achieved by using additives. In the additives process, an object is created by laying down the material in a layer by layer to form a complete 3D object.
Effortless replication and highly accurate complex printing.
Flexibility of working with numerous options in terms of materials, colours, geometrics and design complexities.
Faster realization of prototypes to test product designs and utility as well as pitch to investors.
Flawless 3D objects that replicate the original design.
High productivity is enhanced due to high accuracy of printed 3D objects.
The 3D industrial printer is cost effective for the research and development industry.
The process of printing 3D objects is highly automatic and easy to operate.
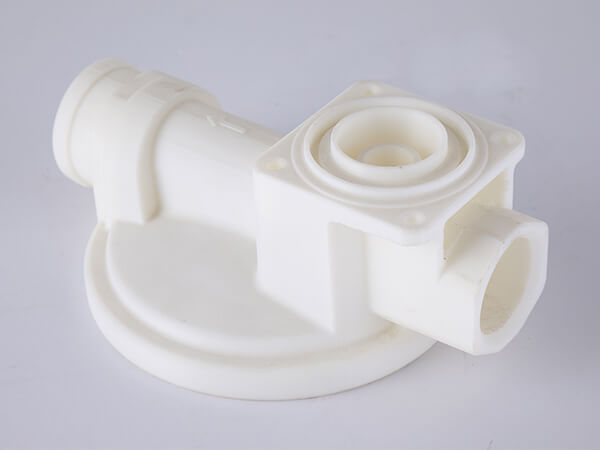
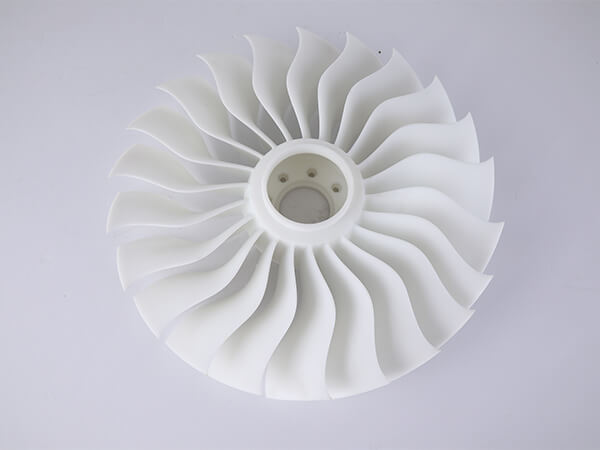
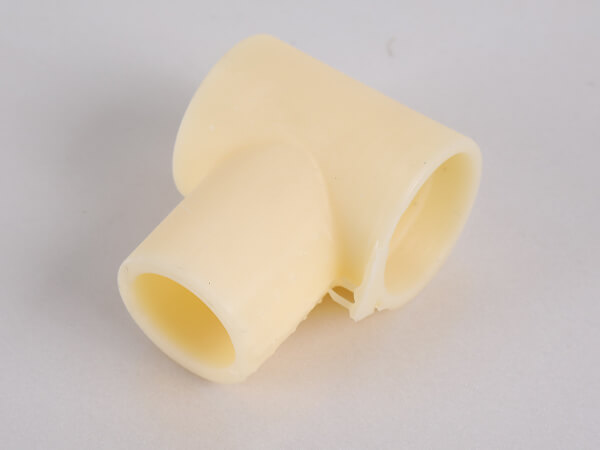
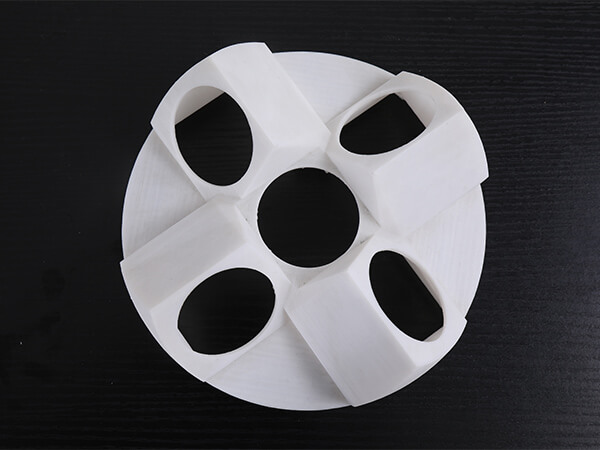
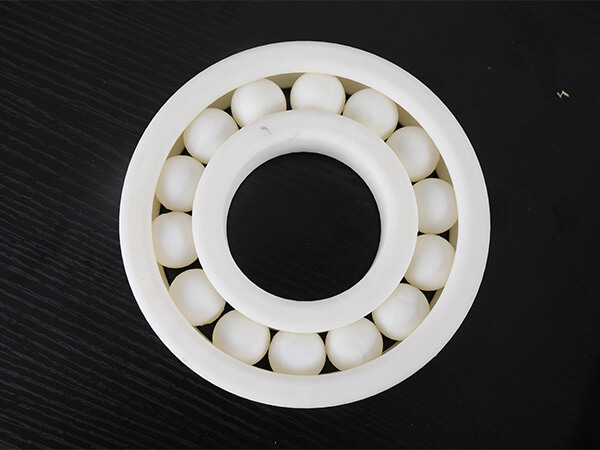
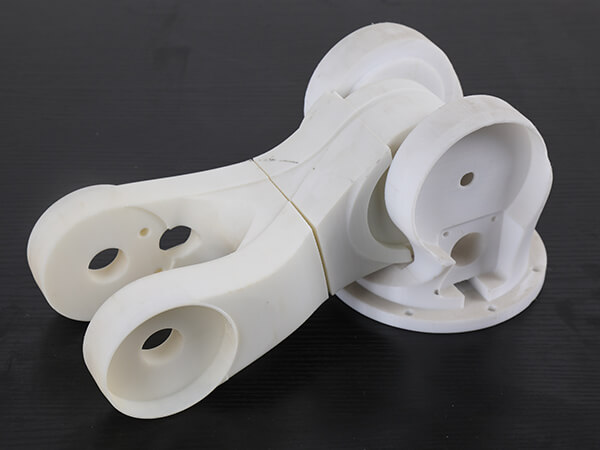
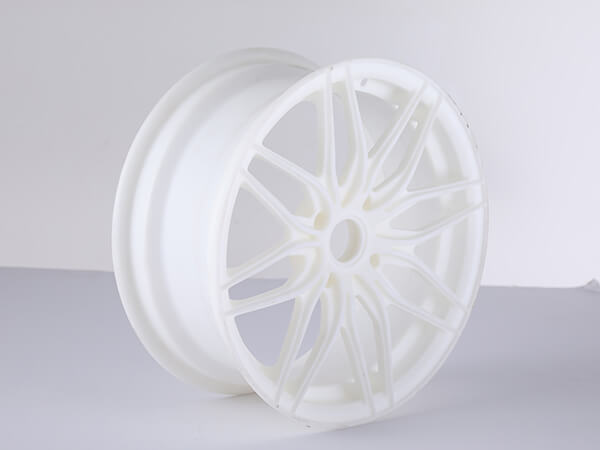
Industrial R&D 3D printers for your Choice
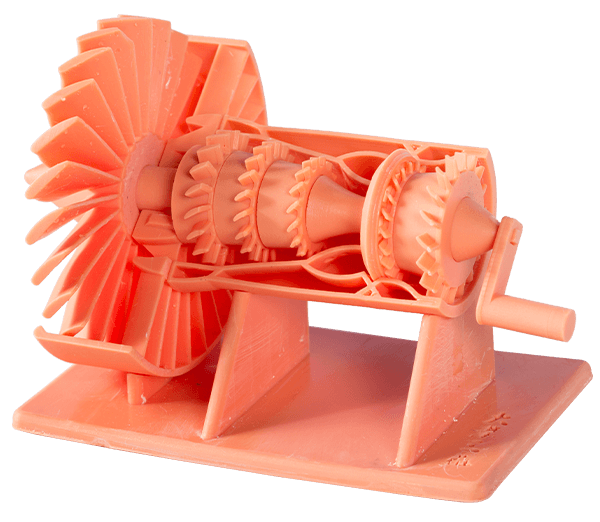
Don't know how to choose a model?
Are you confused about how to choose the correct model and type of 3d printer? We support 24/7.
4 points why choose us
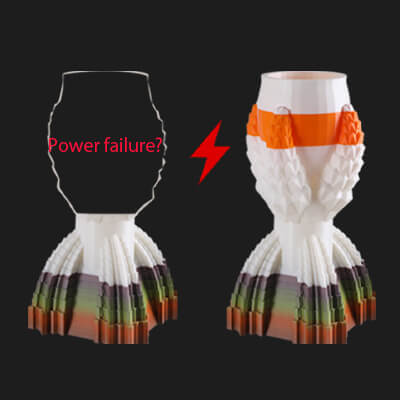
Automatic resume printing
Continue to print the unfinished model after the power is restored when the power fails
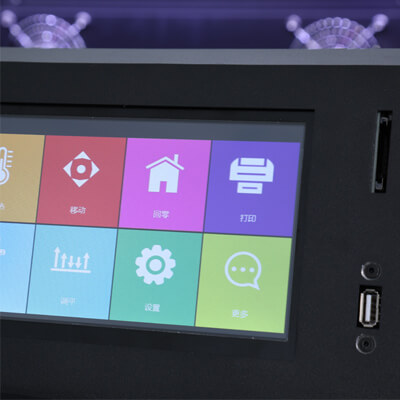
PLC control system
All 3d printers are equipped with PLC control system as standard, makes the operation more convenient, and reduces the error.
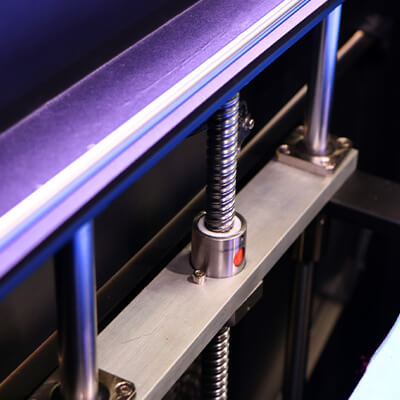
Extremely speed printing
Higher straightness, lower friction coefficient, better smoothness, higher positioning accuracy and more stability during printing.
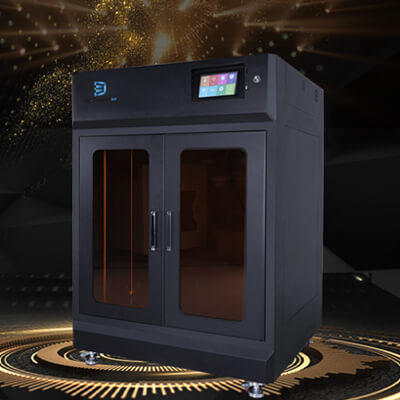
Reinforced structure
The all-metal one-piece shell reduces resonance, makes printing more stable and improves printing accuracy.
What our customers say
How 3D Printers are Used in the Industrial R&D
Industrial R&D 3D Printer Buying Guide
1.1, 1.1What is the Original Production Process of Industrial R&D
1.2, What Processes can 3D Printers Replace?
1.3, What’s the Changes After the Intervention of 3D Printers?
2.1, 3D Printers for Industrial Goods
2.3, 3D Printer for Anime Figure 3D Printer
2.4, 3D Printer for Cosplay and Stage Property
2.5, 3D Printer for 3D Printing Aerospace
The use of 3D printers for industrial R&D has brought about ease of design, efficient production process, and time-saving development procedures to experts in numerous industries. Ranging from hobbyist designing molds for the production of jewelry to experts in aerospace and medical printing, 3D printers have taken a front role.
This buying guide is designed to help you understand the impact and changes industrial 3D printers are having in the R&D industry, the industrial application, materials and the process involved in buying a 3D printer for industrial R&D.
We believe that if you take out time to explore this piece, it would be impossible for you to make the wrong buying decision when scouting for the right 3D printer for industrial R&D.
The Impact and Changes of 3D Printers on Industrial R&D
3D printers for industrial R&D is about to go mainstream in a big way. Most executives and many engineers don’t realize it, but this technology has moved well beyond prototyping, rapid tooling, trinkets, and toys. “Additive manufacturing” is creating durable and safe products for sale to real customers in moderate to large quantities.
Rapid prototyping 3D printing can manufacture parts within hours, which speeds up the prototyping process. This allows for each stage to complete faster. When compared to machining prototypes, 3D printing is inexpensive and quicker at creating parts as the part can be finished in hours, allowing for each design modification to be completed at a much more efficient rate.
High-resolution 3D printers don’t need a lot of space to stock inventory, unlike traditional manufacturing processes. This saves space and costs as there is no need to print in bulk unless required.
The 3D design files are all stored in a virtual library as they are printed using a 3D model as either a CAD or STL file; this means they can be located and printed when needed. Edits to designs can be made at very low costs by editing individual files without wastage of out of date inventory and investing in tools.
3D printers for industrial R&D took many professionals by surprise. However, when it comes to industrial application, not all 3D printers can bring the desired result home. The unique industrial solutions, flexibility, cost-efficient process, and tailored finish FDM 3D printers bring to the table made it a preferred pick by experts in numerous industries.
1.1, What is the Original Production Process of Industrial R&D
Before 3D printers for industrial R&D took over the industrial manufacturing process, numerous modes of traditional manufacturing took the front role. Traditional manufacturing refers to the process of converting raw materials into a finished ready-to-sell product through the use of manual and/or mechanized transformational techniques. The end goal of traditional manufacturing is to add value to achieve the objective.
Traditional manufacturing methods, by contrast, are subtractive in nature. Subtractive manufacturing involves removing parts of a block of material in order to create the desired shape. Cutting wood into useful shapes, for instance, is a very simple example of a subtractive process.
1.2, What Processes can 3D Printers Replace?
3D printers for industrial R&D is set to replace the new development cycle as the system becomes inexpensive. Many companies are already implementing the technology in creating products while centering their attention towards customer feedbacks and customers’ centered designs. The cost of inculcating 3D printers into an R&D production line has reduced drastically, giving room for niche businesses to develop quickly.
Prototyping: Research and development departments require prototypes, oftentimes, a lot of them. In a typical setup, prototypes are handcrafted or made from molds. Before the introduction of 3D printers, R&D experts had to subject themselves to countless hours of design and development procedures due to a lack of adequate innovative equipment for prototyping. But since the FDM 3D printers became a household name to most industry experts, the time, cost, and energy involved in prototyping changed drastically.
Design: it’s impossible to find an innovative R&D team not skilled in the art of creating formidable designs. However, no exceptional design is created by chance; hours of hard work and unwavering dedication goes into the creation. 3D printers for industrial R&D replaced the design phase with real-time 3D models that take away the skepticism and endless questions most designers are subjected to during the design process.
Creating Complex Geometries: needless to say, the basic physical difference in how objects are made with additive manufacturing also produces some major functional differences. The most important of these functional differences is that 3D printers for industrial R&D can be used to create complex geometries that would be difficult or impossible to achieve with traditional manufacturing methods. These complex geometries are often stronger and lighter than their traditionally manufactured counterparts.
1.3, What’s the Changes After the Intervention of 3D Printers?
3D printers for industrial R&D have opened up new opportunities for production, factory maintenance, and R&D. it has bridged the gap between customer intuition, products, and design in numerous industries. From the mode of operation to the way professionals speak design, 3D printers’ intervention in the R&D changed everything.
3D Printers Lowers the Barrier to Entrepreneurship and Product Development: using 3D printers for industrial R&D, businesses can prototype and produce their products using a single piece of equipment, rather than investing in an entire factory setup. In fact, thanks to a host of 3D printing service companies that have arisen in the past several years, small businesses can even make use of additive manufacturing without the initial cost of buying the equipment themselves.
Strong and Lightweight Part: The main 3D printing material used is plastic, although some metals can also be used for 3D printing. However, plastics offer advantages as they are lighter than their metal equivalents. This is particularly important in industries such as automotive and aerospace, where light-weighting is an issue and can deliver greater fuel efficiency. Also, parts can be created from tailored materials to provide specific properties such as heat resistance, higher strength, or water repellency.
Cost-Effective: As a single step manufacturing process, 3D printing saves time and therefore costs associated with using different machines for manufacture. 3D printers for industrial R&D can also be set up and left to get on with the job, meaning that there is no need for operators to be present the entire time.
This rapid prototyping 3D printing process can also reduce costs on materials as it only uses the amount of material required for the part itself, with little or no wastage. While 3D printing equipment can be expensive to buy, you can even avoid this cost by outsourcing your project to a 3D printing service company.
Reduced Waste: We effectively render a material waste by-product when removing it in a subtractive manufacturing process. 3D printers for industrial R&D only uses the material necessary to create a part, ensuring that waste is very minimal. Parts that require support structures for printing, however, will still involve an appreciable amount of wasted material.
Time-Saving: The traditional manufacturing technologies require molds to be manufactured and factories to be ramped up to speed. As a result, it can take upwards of 15-60 days (and sometimes more) to have the first part in hand. For R&D industrial 3D printers, the part can be printed on demand and shipped without any ramp-up or tooling, resulting in a lead time as short as 2 or 3 days.
3D Printers for Industrial Application
In the hands of a skilled engineer, the transition from concept to prototype to the minimum viable product can look a lot like magic, and that’s all thanks to the limitless possibilities 3D printers for industrial R&D are offering. Like we stated earlier, this guide is optimized to help you better understand the function of 3D printers in industrial R&D applications.
To further simplify its impact in the sector thus far, let’s take a quick peek at the opportunities 3D printers are opening up in multiple industrial application fields.
2.1, 3D Printers for Industrial Goods
Industrial goods are based on the demand for the consumer goods they help to produce. Industrial goods are classified as either production goods or support goods. Production goods are used in the production of a final consumer good or product, while support goods help in the production process of consumer goods such as machinery and equipment.
Companies involved in the industrial goods sector represent a variety of industries, including (but not limited to) machinery, construction, defense, aerospace, and housing.
The production of industrial goods calls for heavy capital investment. Most of the companies involved in the production of industrial goods raise capital by issuing shares and debentures and also by resorting to borrowing from financial institutions. However, since the introduction of 3D printers for industrial R&D, the production sequence in the creation of industrial have changed. High-resolution 3D printers have heightened the production line of most manufacturers dealing in the production and distribution of industrial goods.
Has a crucial part broken on your machine? 3D printing spare parts are becoming a huge asset for both companies and customers! With our 3D printers for industrial R&D, you can maintain a digital inventory of your parts and produce them as needed. Moreover, if the part often breaks, it might be time to take advantage of 3D printing to prevent it from breaking! Re-thinking and re-engineering the part can help you improve its resistance over time or to specific constraints.
The industrial goods sector includes companies involved with aerospace and defense, industrial machinery, tools, lumber production, construction, waste management, manufactured housing, and cement and metal fabrication. Performance in the industrial goods sector is largely driven by supply and demand for building construction in the residential, commercial, and industrial real estate segments, as well as the demand for manufactured products.
It’s needless to say that most of the above-listed industries rely largely on the modeling and prototyping operations of 3D printers for industrial R&D makes possible. To keep the rapid prototyping and 3D printing task in line with market needs and customers’ requirements in the industrial goods sector, it’s essential you purchase high-resolution FDM printers. These printers are backed with easy to navigate UI, can print large pieces of stuff, and are quite easy to build and calibrate.
2.2, 3D Printer for Mold
The majority of plastic products in the world today are manufactured by injection molding. However, fabricating molds can be prohibitively expensive and time-consuming. Fortunately, molds don’t always need to be machined out of metal—they can be 3D printed. Here are some of the benefits jewelers, artisans, and the regular day to day 3D printing enthusiast are enjoying from using 3D printers for industrial R&D to print molds.
Printing multiple copies at once: If you’re frustrated that traditional 3D printing necessitates creating one object at a time, 3D printed molds will help you enormously. Although you do have to create one mold at a time, once you’ve got your set ready, you can use them all at once, and mass manufacture your objects in batches that will speed your production nicely.
Starting your own small-scale manufacturing business: If you’re looking to get a one-stop manufacturing business off the ground on a (relatively) shoestring budget, 3D printing your own molds will help you go far. You’ll be able to use the 3D printing and prototyping machine that you have (if you already have access to a 3D printer) or buy it for much cheaper than standard manufacturing equipment if you don’t. Plus, you can start small without worrying about wasting money or resources on much more than you need.
3D printers come in all sizes, from portable and desktop to person-sized floor models, so you’ll be able to tailor your molds to your exact needs and control how much you spend on them. Startup costs can make or break a new business, and 3D printing molds can help you keep those ways down.
Exact copies: If you need consistent replication on a mass scale, high-resolution 3D printers will keep your designs identical without any need to recalibrate between batches. 3D printers themselves are getting more reliable by the second, with both software and hardware updates constantly utilizing the newest ways to talk to each other, but when you 3D print a mold to work with, you only have to worry about design details once. After that, your go-to template will only need adjusting if you want to change anything on purpose, not because you have to compensate for changing printing conditions.
NOTE THAT: 3D printing molds make the printing process simple, time-saving, and cost-efficient. There are a good number of 3D printers for industrial R&D available for the design and creation of molds. While SLA, LCD, and DLP are formidable machines for mold creation, their durability and portability are quite limited. To enjoy the mold design and creation process to the fullest, it’s advisable you opt for the FDM 3D printing process.
2.3, 3D Printer for Anime Figure 3D Printer
Creating animation is a very complex task. From the design phase to prototyping to the end product, you can’t afford to slip out any detail—missing out on even the smallest element can hinder the portability and flexibility of the end product.
FMD machines are regarded as a durable option for creating animations because it grants designers the opportunity to pay meticulous attention to detail while leaving room for even the most minor editing to be carried out. With the best FDM 3D printer at your disposal, you can streamline an animation creation process; rest assured, accuracy is guaranteed.
Animations nowadays are extremely detailed. Many animation lovers find it arguable that every single part, feature, or attribute inculcated in their favorite cartoon characters was detailed down during the design process.
The development process involved in using animations to create a movie is extremely different from having humans act. Unlike humans, animations don’t possess instincts or inbuilt characters—that’s every animation you have ever come across, be it in movies or on social platforms, was thoroughly thought about, detailed, and designed. Imagine the countless hours manually designing an animation would take? Then think of the cost?
The introduction of FDM printers in the animation industry made it possible for designers to create complex elements within a limited time frame. Top FDM printers don’t just make the process faster but also ensures that users get to obtain high-quality end product at a minimal cost.
3D printers for industrial R&D are at the forefront of the cartoon and animation industry, and FDM 3D printers are currently leading the bandwagon. FDM resolution makes it easy for designers and professionals in the 3D printing sector to enjoy a highly detailed printing process.
However, you might want to bear in mind that while FDM 3D printers are ideal for individuals looking to create formidable anime figures in the animation industry, there are multiple variants of custom FDM printers. To ensure you are making use of the right 3D printer for industrial R&D, we recommend you explore our catalog, or better still, put a call through to our support representative today.
2.4, 3D Printer for Cosplay and Stage Property
Creative artists who are using the 3D printing tech to raise the bar on quality cosplay and craftsmanship. Before purchasing the optimal 3D printer for cosplay, enthusiasts must first identify what it is they want to print. Part of knowing what you want to print understands the size of the design, the durability required, and the usage of the print. This makes it easier to decide whether you should go for print volume or resolution, for example.
Typically, Cosplay requires a large build volume because you will be mostly making pieces to be worn. Your home 3D printer will unlikely accommodate large prints, but it may come in handy when you want to print fine details. Printing a large object on a small build area means you will require more welds, and welds are usually a weak point.
There are tons of 3D printers for industrial R&D out there that come with a variety of features, but here are the things to put into consideration when picking a 3D printer for cosplay:
Type of Filament – In most instances, you will find yourself wanting to experience rapid prototyping and 3D printing with different filament colors and types to achieve the diverse characteristics of your cosplay. You will want your prints to be durable and be more realistic, and that means printing with exotic filaments and doing some post-processing as well.
Characters in the Sci-Fi genre, for example, may require the use of more exotic materials like ceramics, metal, and wood, beyond the usual materials like PLA and ABS. For the shields and swords, you may want to consider materials like PCT and PCL. Metallic filaments will be best suited for your metallic finishes or glowing features.
Build Volume – Build volume is the capacity or size of the platform where you will be printing your cosplay. It is one of the most crucial features for a 3D printer for cosplay because you are mostly creating wearable objects. Note that you will need a relatively large build space for most of your costumes or props. The goal is to always go for a volume that can accommodate your print. A large print volume will allow you to print your cosplay in fewer parts, and fewer parts mean that your object will have fewer weak points.
Easy Usage– While a 3D printer for industrial R&D may seem complicated when used for the very first time, it becomes easier to operate with time and experience. Understanding the software and other mechanical features is part and parcel of the learning process. Still, the first few days with your 3D printer can become a daunting task.
If you don’t have a high-resolution 3D printer or maker experience already, you probably want a 3D printer that comes assembled so that you can avoid assembling it from scratch. Many people want to attach a spool of filament and start printing within a matter of minutes. But more importantly, you also want to easily keep track of and control all the parameters that are responsible for the printing process. These may include temperature, print speed, and filament consumption.
Cosplayers have moved beyond the needle and thread into 3D printing technology, which allows creators to bring their favorite characters to life. Today, creators are using a 3D printer for industrial R&D to adapt intricate designs from movies and video games. The first step is choosing the right 3D printer, and we’re here to help you with that decision.
2.5, 3D Printer for 3D Printing Aerospace
Due to the typically short runs of aircraft parts, the aerospace industry uses 3D printers for industrial R&D for a great deal of its production. The technology can produce intricate parts that are more resilient and lightweight compared to those made using traditional techniques, which is an obvious bonus.
Generally speaking, the Aerospace industry was one of the earliest adopters of 3D printing technology, with initial use recorded back in the late 1980s. Nowadays, it is still considered the industry which has the highest rate of adoption of 3D printing technologies.
Factors like quicker delivery of finished parts, relatively low production quantities, and the ability to Design for Additive Manufacturing (DfAM). The latter is especially crucial for producing lighter parts while maintaining strength, addressing challenges like reducing an aircraft’s fuel consumption by reducing its overall weight, thus cutting operational costs and lowering carbon dioxide emissions – two major problems Airlines face.
External factors, which are industry agnostic, like supply chain optimization due to decentralized production of parts in the location they are required (as opposed to centrally producing parts and shipping them around), also make 3D printers for industrial R&D appealing and valuable for players in the Aerospace industry.
In addition, 3D printers for industrial R&D can produce hundreds of thousands of parts without relying on expensive tooling changes involved with traditional manufacturing processes. “Tool-less” production requires less energy since modified parts or upgrades can be produced as needed, alleviating the need for costly storage.
Aerospace parts often include internal channels for conformal cooling, internal features, thin walls, and complex curved surfaces. 3D printing processes can create highly complex and lightweight structures with high stability whilst allowing for the consolidation of multiple parts into a single component.
Note that, Prior to production, tooling for injection molding, jigs/fixtures, and thermoforming can be manufactured quickly and at a lower cost thanks to 3D printers for industrial R&D. While 3D printing in the aerospace industry used to be used for the prototyping phase alone, it is now used more than ever for the manufacturing of end parts too, since larger industrial printers can print quickly using a variety of materials.
2.6, 3D Printer for Car Parts
The 3D printing technology has given rise to spectacular achievements in the automotive industry, starting from the possibility of fast prototyping, through a more and more widespread production of final car parts, and ending with 3D manufacturing of nearly the whole cars.
Nobody should be surprised with a growing interest in 3D printers for industrial R&D on the part of large concerns, such as Mitsubishi Chemical or BASF, which see a serious and profitable business in using FDM printing technology in the automotive sector.
The automotive sector has liked rapid prototyping 3D printing and has been using its opportunities on a daily basis more and more often. Designers and engineers open to innovation implement bold ideas with the use of the technology, thus, extending the pallet of engineering benefits and optimizing the manufacturing processes.
3D printers for industrial R&D has great power and enables the achievement of effects that would not be possible with the use of traditional manufacturing methods. Car components produced with the FDM technology are lighter, which results in a reduction of the vehicle weight, better performance, and lower energy consumption.
One of the currently most popular and most frequently used 3D printing technology in the automotive sector is FFF (Fused Filament Fabrication). Its advantage is the possibility to use many different materials, the properties of which are similar to plastics.
With the use of a 3D printer for industrial R&D, the needed parts and details may be created, which not only enables companies to keep production continuity, which is very important nowadays but also become independent of external suppliers and streamline the production processes.
If you are in search of high-resolution 3D printers that can effectively streamline the FDM 3D printing process in the design and creation of auto parts, we recommend you take a look at the variants available in our catalog.
2.7, 3D Printer for Medical
3D printers for industrial R&D has many functions in a variety of industries; however, in the medical field, it has four main applications. Rapid prototyping 3D printing could be used to replace human organ transplants, speed up surgical procedures, produce cheaper versions of required surgical tools, and improve the lives of those reliant on prosthetic limbs.
Additive manufacturing, otherwise known as 3D printing, was first developed in the 1980s. It involves taking a digital model or blueprint of the subject that is then printed in successive layers of appropriate material to create a new version of the subject.
The technique has been applied to many different industries, including medical technology. Often medical imaging techniques, such as X-rays, computed tomography (CT) scans, magnetic resonance imaging (MRI) scans, and ultrasounds, are used to produce the original digital model, which is subsequently fed into the 3D printer. Here are some of the product design 3D printing brings to the table in the medical industry.
3D printing of surgical instruments: sterile surgical instruments, such as forceps, hemostats, scalpel handles, and clamps, can be produced using 3D printers. Not only do high-resolution 3D printers produce sterile tools, but some are also based on the ancient Japanese practice of origami, meaning they are precise and can be made very small. These instruments can be used to operate on tiny areas without causing unnecessary extra damage to the patient.
Custom-made prosthetics using 3D printing: 3D printing in the medical field can be used to produce prosthetic limbs that are customized to suit and fit the wearer. It is common for amputees to wait weeks or months to receive prosthetics through the traditional route; however, 3D printers for industrial R&D significantly speeds up the process, as well as creating much cheaper products that offer patients the same functionality as traditionally manufactured prosthetics.
Replicate Organs: Another application of 3D printers for industrial R&D in the medical field is creating patient-specific organ replicas that surgeons can be used to practice on before performing complicated operations. This technique has been proven to speed up procedures and minimize trauma for patients. This type of procedure has been performed successfully in surgeries ranging from a full-face transplant to spinal procedures and is beginning to become routine practice.
2.8, 3D Printer for Architectural Models
If you are a modern-day architect, you might be familiar with using computer-aided design (CAD) software to create virtual 3-dimensional(3D) objects for projects. If you have been around for some time, you will know that these models don’t mean much if your clients can’t touch and interact with them. Designing physically scaled models of your virtual 3D objects is a better way to visualize your architectural ideas. This is where a 3D printer comes in very handy.
3D Printers for industrial R&D acts as an intermediary between you as the designer and the manufactured 3D object you desire to showcase to your client or colleagues. It does so by translating your CAD project into a 3D object. The process is much faster than traditional model making methods that rely on very skilled craftsman to create a scale model. You will definitely save a lot of time when using a 3D printer but also leave your client very impressed with a good quality scale model.
3D printing for architecture is a growing application of additive manufacturing. You can realize concrete structures and 3D printed houses. Having a physical architectural model will enable you as an architect to better present your ideas and come across clearer to your client. The level of detail high-resolution 3D printers adds to your scale model can be very impressive when you try to win a client over.
While it is useful to have models and mockups, a physical model makes it easier to spot a design flaw or any defects associated with your design. The low cost of creating 3D models and the amount of time saved makes it better than traditional methods used to create scale models.
Innovation is encouraged by 3D printers for industrial R&D. When you are able to witness the creation of your idea into a real object in a few hours, it is much easier to go and create something new again and improve on that design. If you want to experiment with different designs; this way, model creation allows that. This way, you can make sure you only present the very best and most creative ideas to your client.
Don’t miss out on the unique opportunities the FDM 3D printing process brings to the architectural industry. If you are in search of a high-resolution 3D printer for industrial R&D that can cater to your printing line and would like to be on the safe edge, contact Dreambot3D support team today; we will guide you through the buying process.
2.9, 3D Printer for Drone
What’s the benefit of using 3D printers for industrial R&D to print drone parts? If you’re not an experienced RC pilot, crashing and breaking parts of your aerial vehicle can be expensive. Instead of buying new parts at a hobby shop, you can 3D print your own spare parts as needed.
For different use cases, different designs will prove worthwhile. For the hobbyist that buys a fully assembled quadcopter, they’ll still appreciate a simple 3D printed range booster that, acting as a parabolic reflector with some metallic tape, will increase the range of the remote control threefold.
Elsewhere, the tech enthusiast that builds his own drone from scratch can improve the accuracy of his onboard electronics by eliminating general shakiness with a 3D Printed Anti Vibration Mount, which still conducts major movements that come from actual changes in flight.
However, you might want to note that 3D printing takes time. It can take up to several hours to print a small-sized part of sufficient quality. Moreover, becoming an expert in 3D modeling and high-resolution 3D printing requires skills you have to develop and practice. In the early stages, a beginner may experience frustration when designing the parts they need.
But don’t worry, there are plenty of tutorials online, plus websites where you can find STL files of 3d printable drone parts, which you can download and print without having to create them yourself. Other than the above, there aren’t many reasons why you shouldn’t just go ahead and 3D print your own parts!
With your own 3D printer for industrial R&D to hand, part designs can be easily upgraded and further developed to improve the performance of your quadcopter. On top of that, 3D printed drone parts are quickly interchangeable, and you can do it yourself. You can even have the parts manufactured by a professional 3D printing service – if you want to get the best price for a special item, please consult the Dreambot3D support team.
2.10, 3D Printer for Gun
Generally speaking, most 3D printable gun files still require non-3D printed parts in order to complete the build; otherwise, they’re not all that reliable – making them a less than ideal option for would-be criminals looking to have an unregistered firearm.
But, this is changing, and a lot of improvements have been made to 3D printers for industrial R&D. Many manufacturers now provide FDM machines capable of effectively 3D printing gun parts such as AR-15 lowers, Glock frames, AK receivers (which can handle 2,000 rounds and are only partially 3D printed), and some pistols like the Songbird (which is primarily 3D printed).
Part of their goal is to allow people to 3D print guns as cheaply as possible, using the cheapest 3D printers and filaments. While the former gun parts (Glock frames, AK receivers, etc.) still require a host of metal parts to be completed, the latter does not.
Many industries that use 3D printing to build their own guns are moving away from 3D printing them and shifting to using CNC milling instead. Rather than trying to print an entire gun out of plastic, these groups are milling unfinished lower receivers for AR-15s, known as the 80% lowers or 80% receivers, and using that along with other parts to produce completed rifles.
With these CNC milled guns, after buying the CNC mill itself, you can spend about $200 to $400 more for the additional gun parts. However, using 3D printers or industrial R&D to design guns is a more probable option. The fast and efficient FDM 3D printing process backed by the simple and easy to model product design 3D printing brings to the table makes it a cost-efficient option.
How to Choose Materials
There is a lot of confusion about choosing the right FDM material for 3D printing. Every material has a different set of properties, which make it suitable for certain applications while unsuitable for others. For example, concept prototypes are used only for display purpose and not for functional testing so using a material which is simple to print with is the correct choice instead of going for a strong material which is difficult to print with.
When it comes to choosing the right FDM 3D printer material, you need to put a lot of factors into consideration. Ease of use, strength, durability, flexibility, heat resistance, aesthetics, and complexity of print are amongst the many factors you have taken into consideration.
To help you easily select a suitable filament for your 3D printer for industrial R&D, below is a list of the most notable materials available, with sustainable information on the features and benefits attached to using them in your rapid prototyping 3D printing task.
3.1, PLA
PLA filament is by far the most popular FDM 3D printer material, and there’s a good reason for that. It comes in many shades and styles, making it ideal for a wide range of applications. Whether you’re looking for vibrant colors or unique blends, it’s an easy-to-use and aesthetically pleasing material.
PLA is short for Polylactic Acid, a thermoplastic polymer that is derived from renewable resources, more specifically from corn starch or sugar cane. This sets the material apart from other commonly used plastics, which are procured through the distillation and polymerization of non-renewable petroleum reserves.
Since PLA filament is a biodegradable product, it tends to naturally break down in about three to six months. Other thermoplastic materials can take up to a thousand years to decompose, making PLA much more environmentally-friendly.
PLA material has been thrust into the spotlight by the rise of custom FDM printers. PLA filament is available in a wide variety of colors and blends, and innovative PLA-based materials seem to be constantly hitting the market.
Outside of 3D printing, PLA is also used to produce things like medical implants, food packaging, and disposable tableware. But inside of the FDM 3D printing sphere, PLA filament is widely thought of as an aesthetic material best used for prototyping.
3.2, ABS
As a thermoplastic polymer, it can melt and cool without altering its chemical properties. That makes it an interesting FDM 3D printer material. The filament is known to be strong, tough, and durable. It is also forgiving to scratches, offers good resistance to heat and everyday chemicals.
It can endure heat, pressure, and stress like no other 3D printer for industrial R&D material, making it a great choice for wear and tear prints. You can try this out yourself: If you move a strain of ABS filament, it will distort and bend before breaking.
PLA breaks much more easily. ABS is quite forgiving, as long as you print with the right settings and proper temperature management. You can even achieve overhangs of around 45 degrees. If the print succeeds, the results are very convincing.
Most makers like the material because you can process its surfaces with acetone, glue parts, and even file off some material. Lastly, it can be easily painted with acrylic colors. ABS filament is not toxic when 3D printed. Only at very high temperatures (400 °C), the material decomposes into butadiene (which is carcinogenic to humans), acrylonitrile (possibly carcinogenic to humans), and styrene—nothing you want to inhale under any circumstances.
If you don’t have a 3D printer at hand, you can have ABS parts printed by a professional 3D printing service. You can put a call through to our support representative to obtain the best deal on a high-resolution FDM 3D printer for industrial R&D.
3.3, Nylon
Nylon (a.k.a. Polyamide) is a popular material in the plastics industry, known for its toughness and flexibility. Nylon filaments typically require extruder temperatures near 250 ºC. However, some 3D printers for industrial R&D allow printing at temperatures as low as 220 ºC due to their chemical composition.
Many printers do not include a hotend that can safely reach 250 ºC, so these lower-temperature versions can be useful and potentially save you from needing to upgrade your hotend. One big challenge with Nylon filaments is that they are hygroscopic, which means they readily absorb moisture from their surroundings.
Printing Nylon after it has absorbed moisture will lead to several print quality issues; thus, filament storage becomes very important and requires special attention. Some of the Pros of using Nylon filament on your custom FDM printer include;
- Tough and partially flexible
- High impact resistance
- No unpleasant odor while printing
- Good abrasion resistance
Cons of Nylon Filament
- Prone to Warping
- Air-tight storage required to prevent water absorption
- Improperly dried filaments can cause printing defects.
3.4, Carbon Fiber
Carbon fiber filaments are composite materials formed by infusing fragments of carbon fiber in a polymer base, similar to metal-infused filaments but with tiny fibers instead. The polymer base can be of different 3D printing materials, such as PLA, ABS, PETG, or nylon, among others.
While true carbon fiber materials have long continuous fiber strands that improve mechanical resistance, these FDM 3D printer materials contain short particles of around 0.01 mm in diameter. Although this is enough for improving the strength of printed parts, keep in mind that such filaments cannot compare to the actual material.
For those seeking tougher FDM 3D printer materials, carbon fiber filament presents a relatively easy alternative to the more expensive and demanding materials, such as polycarbonate (PC) or PEEK. Moreover, the increased strength provided by the carbon fiber particles contributes to greater dimensional stability, helping to avoid warping and shrinking.
However, using a 3D printer for industrial R&D to 3D print these materials does present some issues. The infused carbon fiber particles aren’t melted by the nozzle during extrusion, which may lead to frequent clogging. In addition, these particles work as abrasive agents during extrusion, which over time will wear down a brass nozzles’ internal bore. This is why special nozzles like hardened steel are strongly suggested for printing with composite materials.
PROS
- Increased strength and stiffness
- Good dimensional stability
- Overall nice surface finish
- Lightweight
CONS
- Frequent clogging
- The abrasive filament that wears down brass nozzles (requires special hardware)
3.5, PC
Polycarbonate (PC) is a powerful material used in 3D printers for industrial R&D. It stands out for three main features: optical clarity, resistance to heat, and incredible toughness. This makes it perfect for use in DVDs, safety glasses, riot shields, and even bulletproof glass.
3D printing with variants of PC will typically get you a temperature resistance of just over 110 °C, yielding translucent, icy prints. Some brands offer a small range of different colors and blends, though variants are more limited than for the more aesthetically-oriented materials like PLA.
Parts printed with PC filament will come out fabulously strong, but printing with this FDM 3D printer material can be quite a challenge. As with any filament, check the manufacturer’s recommended settings before printing, but some general settings are outlined below, followed by some troubleshooting tips.
PC’s extreme resistance to heat calls for equally extreme temperatures. An all-metal hot end and a heated bed are mandatory, and printing in the controlled environment of an enclosure is highly recommended. Part cooling should also be turned off to ensure proper interlayer adhesion. Keep in mind that this material is designed to be functional (as opposed to aesthetically pleasing), which means the print quality may suffer.
PC also has a strong tendency to ooze during the rapid prototyping 3D printing process. Tune your retraction settings but avoid retraction distances of over 10 +mm to prevent jamming. If your hot end doesn’t get hot enough, start printing at slower speeds. But a warning: the material generates strong fumes and odors. Always print PC enclosed or in a well-ventilated area.
3.6, PETG
PET (polyethylene terephthalate) is a thermoplastic polymer used for drink bottles or sailcloth. Mixed with glycol (hence the “G”) exhibits good 3D printing features. PETG FDM 3D printer material is resistant to high temperatures and water, presents stable dimensions, no shrinkage, and good electrical properties.
PETG combines ABS durability and PLA printability, and it comes as no surprise that it’s frequently chosen by professionals seeking a reliable filament for their projects. PETG gained a lot of recognition during the coronavirus pandemic because it can be easily sanitized and therefore is useful for medical applications such as face shields.
Note that You may encounter two options — PETG (sometimes written as PET-G) and PET. The “G” stands for glycol — a substance added to prevent corrosion and crystallization effects. Glycol modified PET is easier to 3D print. PET without glycol is more fragile and prone to breaking.
On the other hand, PETG is characterized by a delicate outline that’s easy to scratch. That being said, the chemical properties of PETG are far better for 3D printing despite some minor disadvantages. PETG is suitable for use on any 3D printer for industrial R&D.
However, if you are interested in created 3D prints with PETG and you are yet to find a suitable high-resolution 3D printer for the task, don’t hesitate to put a call through to our support team.
3.7, PVA
Polyvinyl alcohol, or PVA, is a water-soluble polymer, not to be confused with PVAc – polyvinyl acetate – which is water-soluble white glue. PVA is a colorless, odorless synthetic polymer with significant biocompatibility properties. It’s also low-toxicity, so able to be used in health products such as contact lens solution, and reasonably biodegradable.
PVA is best known within the rapid prototyping 3D printing community as a support material used with multi-extruder 3D printers.
Normally, FDM machines have only one extruder, and both the printed part and support structures are created using the same material. Removing supports can be a tricky job depending on their location, not to mention the ugly marks they can leave on the part.
Dual-extrusion FDM printers, on the other hand, allow for the use of different materials for the part and supports, and this is where PVA comes in handy. The biggest advantage of PVA filament is that it dissolves in water, so support structures printed with this material can be effortlessly removed by simply emerging the part for a few hours.
This method not only facilitates support removal but also prevents any marks from being left on the part and reduces the need for post-processing like sanding and painting. Great solution, right? Sadly, it’s not that simple. Dual extrusion can be quite tough and takes lots of calibrating to finally get quality 3D prints.
PVA generally works well with PLA filaments since it uses similar printing conditions, including temperature. PLA is a hydrophobic material, meaning it doesn’t “like” water, so if a PLA part is printed with PVA supports, only the supports will dissolve in water, leaving the part in perfect condition.
3.8, TPU
Thermoplastic polyurethane, or TPU, is a very common form of elastic polymer, or elastomer, capable of being used on any properly-equipped FDM 3D printer. Of the many kinds of flexible FDM 3D printer material, TPU is slightly more rigid than others, making it easier to extrude and use. It’s a medium-strength material with very high flexibility and durability, able to withstand much higher compressive and tensile forces than its more common counterparts PLA and ABS.
When printing, TPU exhibits minimal warping and shrinkage and, like PLA, doesn’t require a heated bed, although it is recommended. The ideal print temperature is between 210 and 230 °C, but this may vary from one manufacturer to another.
TPU doesn’t produce any notable levels of fumes while printing, but it’s not considered to be food safe. And though it’s a non-soluble material, it is hygroscopic, meaning that it will slowly absorb moisture from its surroundings, degrading over time.
One downside to TPU is the printing speeds, which are rarely higher than 30 mm/s. This is because it’s difficult to push the proper amount of filament through the hot end, resulting in prints taking a lot longer to complete. You can use any FDM 3D printer for industrial R&D to create formidable prints using TPU.
3.9, HIPS
High impact polystyrene (HIPS) is a material blend of polystyrene plastic and polybutadiene rubber. The mixture of these polymers results in a material that’s both tough and flexible.
HIPS is an FDM 3D printer material very similar to ABS, but as the name implies, it’s capable of withstanding much higher impact forces. It’s easily painted, machinable, and works with a large number of adhesives. Moreover, it’s food-safe, being declared FDA-compliant for food processing applications.
During the FDM 3D printing process, HIPS is mostly used as support material since it dissolves in limonene solution, eliminating the need for removal via abrasives, cutting tools, or any other such things that leave your print less-than-perfect. Limonene is a solution made with lemon peels and can be easily obtained. This solution, however, can potentially damage 3D printing materials other than ABS.
This is one of the reasons why HIPS is best paired with ABS. The other reason is that the printing temperature range is very similar between these materials, making the difficult task of dual-material 3D printing easier.
One rather unfortunate quality that HIPS shares with ABS are that it releases toxic fumes when heated. When using a 3D printer for industrial R&D to design a model, HIPS releases small amounts of styrene into the atmosphere. It’s highly recommended to place the printer in a well-ventilated area when using this material.
3.10, ULTEM
Filaments made from ULTEM™ 9085 resin offers the ability to create parts with excellent properties at elevated temperatures due to a high glass transition temperature (Tg) of 186°C. PEI is an amorphous, high-performance polymer that combines excellent thermal properties, exceptional dimensional stability, inherent flame retardancy, and good chemical resistance.
ULTEM’s tensile strength is 15,200 psi, and it has a flexural modulus of 480,000 psi. It has very high heat resistance, maintaining most of its physical properties in temperatures as high as 170°C. Additionally, it has high dielectric strength and can go through thousands of cycles in a steam-based sterilization autoclave without degradation. Its strength-to-weight ratio is also quite similar to that of aluminum, and it can be machined with conventional metalworking tools.
Those mechanical and thermal properties are ideal for a number of demanding applications, from aerospace to medical to electrical. Indeed, ULTEM holds several aerospace certifications and is FDA compliant. In planes and rockets, ULTEM is used in ventilation systems, latches and hinges, and cable ducts.
Medical professionals and research scientists often use instruments made from the material, and electrical component manufacturers use ULTEM in connectors, insulation parts, and chip test sockets.
Research on the Advantages of 3D Printers Compared to Traditional Processes
3D printers for industrial R&D have taken over workflow in almost all industries. While the remarkable opportunities attached to introducing the rapid prototyping and 3D printing process to your production line is priceless, a lot of artisans, jewelers, hobbyist, and professional R&D teams are still skeptical about making the necessary investment.
To help you better understand the advantages of high-resolution 3D printers bring to the table, let’s take a look at some of its advantages in comparison with traditional processes.
Cheaper for small production runs
Traditional manufacturing like injection molding requires mass production to even out the overhead cost of tooling, labor for assembly, and production (an injection mold can cost thousands of dollars). On the contrary, with 3D printers for industrial R&D, the cost of manufacturing one item stays the same no matter what the quantity is, making it cheaper when the quantity is small.
More customizable, More adaptable
Because the cost is the same for each added unit, it is possible to make an unlimited amount of changes to the product; high-resolution 3D printers can be used for prototyping: you’d use 3D printing to make a prototype and update the prototype until satisfaction. This is a crucial step before getting the product to mass production. 3D printers for industrial R&D can also be used during the rest of the manufacturing process to create unique pieces that can be more responsive to your needs, progress in conception, and consumer feedback.
No Added Cost for Complexity
Creating complex mechanical constructions via traditional manufacturing requires precision and skills, especially for the assembly of complex parts, which means that price increases with complexity. It is not the case with 3D printers for industrial R&D, which creates an entire piece in one process instead of creating each component before assembling. Therefore, there is no added cost for complexity.
Avoid Waste
3D printers for industrial R&D is incredibly resourced efficient since the only material consumed is what passes under the laser (or through the extruder, etc.), whereas traditional manufacturing requires the use of extra materials (molds for injection molding, scraps for perforated sheet metal assembly, etc.). The fact that manufacturers don’t have to produce as much of a given product to justify the setup costs also reduces waste.
The Reduced cost of failure Means Enhanced Innovation.
Customizability means that if the initial prototype isn’t satisfactory or if a change needs to be made after market launch, it won’t occasion great adapting costs as it would with traditional manufacturing. 3D printers for industrial R&D allow to take more risks and, therefore, to be more innovative.
4.1, Introduction to the Working Principle and Development History of 3D Printers
What’s almost 40 years old but looks brand new? Believe it or not, it’s 3D printing. Yep, additive manufacturing technology has been around since the Reagan era. At the time of invention in the 1980s, 3D printers focused on creating scale models using computer-aided design (CAD). The first patent for a 3D printer was issued to Charles Hull for “Apparatus for Production of Three-dimensional Objects by Stereolithography” in 1986. Hull went on to start the first 3D printing company, 3D Systems Corporation.
With this background in industrial manufacturing, most 3D printing technologies were protected by patents held by companies in the industrial market. As patents expired, 3D printers geared for the consumer began to appear.
3D Printers for industrial R&D have existed since the 1980s; however, it was not until the expiration of Stratasys’ patent in 2009 protecting their ownership of the fused deposition modeling (FDM) process that affordable consumer thermoplastic extrusion printers proliferated. The expiration of subsequent patents covering alternative additive manufacturing processes has further fuelled this growth.
4.2, Analysis of the Advantages of Using 3D Printing in Industrial R&D
Research & Development is a very crucial part of many industries as well as markets; it has its own benefits. Manufacturers and firms need to ensure that their products constantly evolve and meet the ongoing trends, changing market demands, challenging competition, varying consumer requirements, and at the same time, be cost-efficient.
R&D is a forward-looking step that forms the foundation for the product innovation lifecycle and is also the precursor for future product development and market expansion. The use of 3D printers in industrial R&D has reshaped the way experts and professionals in multiple industries think design and prototyping.
From how cars are made to the design sequence in aerospace and the continuous innovation technology brings to the table, 3D printers for industrial R&D plays a crucial role. Here are the major benefit having a custom FDM printer in your production line offers;
- Design iterations – Effortless replication and design modifications.
- Flexibility to work with numerous options in terms of materials, colors, geometries, and design complexities.
- Faster realization of prototypes to test product designs and utility as well as to pitch to investors.
- Flawless products that are true replicas of the designs to the minute detail.
How to Choose a 3D Printer to Make You Gun and Gun Model
The type of 3D printer you can choose to make you a gun depends on numerous factors. Apart from the design and styling you desire your gun to have, factors such as budget, type of 3D printer, resolution, safety configuration, and a handful of other factors need to go into consideration.
However, it’s important to note that not all 3D printers can effectively help you 3D print a gun. To 3D print a gun, you need a high-resolution FDM 3D printer and, in some cases, a scanner. In the following sections, we would look at the 3D printer for industrial R&D needed to 3D print a gun and the factors that need to be put into consideration if you are looking to pick the right custom FDM printer for the job.
5.1, Which Machines are Needed and For What Purpose
Like you already know, 3D printers for industrial R&D comes in different variants and are optimized to perform a different task. LCD, DLP, and SLA 3D printers are regarded as resin-based 3D printers. These printers are compatible with 3D printing tasks that involve designing or modeling resins into the desired shape.
However, when it comes to 3D printing guns, resin is not as portable nor palatable as filaments. And when trying to 3D print filaments, FDM 3D printers are the most compatible. Below is a brief explanation of the working principle behind the FDM 3D printer.
5.1.1 FDM 3D Printer
Fused Deposition Modeling (FDM) is used to form prototype parts made of waxes and polycarbonates but often doesn’t yield as much detail as SLA. A continuous filament of molten thermoplastic material is fed from a coil through a printer extruder head and forced out of a nozzle onto a flatbed.
Controlled by a computer, the machine head moves in two dimensions to form each layer of the part. Hobbyists often use custom FDM printers for modeling small parts and restructuring mannequins, while manufacturers also use them for creating parts that are heat resistant and can withstand intense functional testing.
There are numerous variants of FDM 3D printers for industrial R&D available. If you are looking for a custom FDM printer that can accurately cater to your printing needs, we recommend you explore our catalog or put a call through to our support representative today.
5.1.2 3D Scanner {optional}
3D scanning is the process of analyzing a real-world object or environment to collect data on its shape and possibly its appearance (e.g., color). The collected data can then be used to construct digital 3D models. A 3D scanner can take almost anything and digitize it. Using special software and a scanner, an object can be “captured” as a digital image by taking measurements from light bouncing off of the object.
Note that the involvement of 3D scanners in the gun 3D printing process is optional. You can accurately 3D print a gun with a custom FDM 3D printer for industrial R&D without making use of a 3D scanner.
5.2, How to Choose an FDM 3D Printer
It wouldn’t be proper if we conclude this 3D printer for industrial R&D buying guide without providing information to help you guide your buying decision. When buying an industrial 3D printer for R&D, there are a few factors you need to first place into consideration. Below is a slight breakdown of the necessary factors.
5.2.1 What is the size of the Print
Determining the size of a print requires in-depth knowledge of the customer base or audience you create 3D models for on a regular. If your day-to-day workload revolves around using 3D printers for industrial R&D to provide CAD designs and models of large print size to experts in numerous other industries, we recommend you thoroughly scout for a machine palatable enough to handle the dynamic needs of your customer base before finalizing the purchase.
5.2.2 Choose a Reliable Brand
While it’s important you choose the right 3D printer for your industrial R&D need, the process involved can sometimes get confusing. There are tons of brands and limited review sites to help you pinpoint which is more reliable. To be on the safe edge, you need to carry out a brand review yourself; here are some questions to rely on during the brand scouting process;
- For how long has the manufacturer you are about to purchase a 3D printer from been in business?
- What sort of customer feedback is backing up their brand’s identity?
- Are they regarded as a top brand by professionals and experts in the industry?
- How often do they provide jewelry 3D printers with a price tag in line with the productivity, efficiency, and durability you require from the device?
5.2.3 Safety Configuration of the Machine
Safety comes first. Be cautious not to buy something that might bring your business trampling to the floor. Most people don’t bother to check the safety measures when using a particular 3D printer for industrial R&D. Don’t make that mistake. Make sure you understand the safety configuration of the machine. If you are new to that top filament printer, follow all the instructions given in the guide. Machines differ.
You now ready to purchase an FDM 3D printer of your choice. Try to know your needs and your clients’ as well, check the print size and the thing to be printed, research on the brand and its technical support, Purchase within your budget and check the configuration of the machine.
5.2.4 Resolution Requirement of the Machine
FDM 3D printers come in different variants, shapes, and sizes, optimized with a fitting design and resolution. At Dreambot3D, our daily task revolves around catering to individuals’ dynamic needs and desires from numerous parts of the globe. We know how daunting navigating a machine with a proper resolution can be.
Dreambot3D core value is to provide satisfactory all-round services. To keep up with this mission, we offer a support team that can help you understand the resolution requirements of multiple 3D printers for industrial R&D, the industries they are optimized to serve and direct you towards multiple variants that would serve you better.
5.2.5 Consider Weather, the Price of the Machine, is Acceptable
Anything available for purchase has a price. It’s up to you to decide if the price is within your means. Top 3D printers for industrial R&D, too, have a price range. The prices vary with needs and want. If you want a luxurious printer, it will cost you accordingly. Checking the price of the printer model before heading to the counter will save you heartache.
FDM 3D printer is a low-cost resin 3D printer; however, it’s still expensive. Checking the cost of a printer should be considered even if it comes last on your list. Don’t wait for those cashier embarrassment; go for a filament-based printer that will fit in your budget.
5.2.6 Consider the Suppliers After-sales Service Capability
Making a purchase is one thing; enjoying the benefit of your purchase to the fullest is another. The best FDM 3D printer always requires a sizable investment, and we are certain you wouldn’t want to make such an investment from a supplier with little to no track record of authenticity or credibility in the industry.
To avoid making such a mistake, take into consideration the technical support service offered. Every 3D printer for industrial R&D supplier should provide a minimum of 12 hours of technical support service Monday to Friday. However, there are a lot of reputable companies providing 24 hours technical support 365 days a year.
5.2.7 Consider the Service Life of the Machine
The service life for most industrial 3D printers for R&D is about 5 to 10 years. While the warranty policy on most 3D printers doesn’t grant you access to refunds or after-sales privileges 1 or 2 years after purchase, purchasing an industrial 3D printer from a reliable manufacturer comes with the guarantee that your machine will be in shape and keep your production line running for at least five years.
With that being said, it’s important to note that the estimated service life of a high-resolution 3D printer can change at any time based on external factors. How you use your machine determines how long it would last. If you leave your industrial FDM 3D printer packed dirty on a regular, you shouldn’t expect the ten years life expectancy to hold any ground.
5.2.8 Consider the Maintenance Cost of the Machine
Using 3D printers for industrial R&D to print for hours can cause some mechanical parts to lose their grip or hold to the machine; some might degrade after months of being used. If not upgraded, the final quality of your prints will consequently reduce.
Machine maintenance is necessary, and it might come with added costs where some parts like the nozzle may need to be replaced entirely. You must incur a reasonable maintenance cost of your machine to consistently get clean and fine detailed prints.
Dreambot3D is a 3D printer manufacturer that defied the odds by manufacturing 3D printers for industrial R&D that are highly versatile, cost-effective, easy to use and maintain while still giving you high detail prints. If you are interested in finding out which 3D printing equipment is best suited for your needs, get in touch with our support team today.
Conclusion
This is the point where we draw the curtains. We have talked about all there is to discuss pertaining to industrial 3D printing and the processes involved. We believe you are well equipped with all the information you need to make a reputable buying decision.
However, this piece wouldn’t be complete if we don’t bring to your notice the one-stop printing solutions our 3D printers for industrial R&D are optimized to provide.
When it comes to choosing a reliable 3D printer for industrial R&D, you need a supplier with an indisputable track record. With numerous industrial 3D printer manufacturers priding themselves with the banner of top-notch highly efficient printers, it’s hard to detect which company offer low-cost, high-resolution 3D printers that actually possesses such attribute.
At Dreambot3D, we provide 3D printers for industrial R&D capable of providing a one-stop solution for dental printing, medical printing, aerospace, tech, automotive, etc. Regardless of your industry and your 3D printing needs, you can put a call through to our support service; rest assured, we have a machine capable of handling your every need.