3D Printer for Aerospace
3D printing aerospace components is possible using Dreambot3D 3D printers. The aerospace industry highly makes use of 3D printers to print strong, detailed and durable parts better than traditional manufacturing.
How 3D printers work for Aerospace
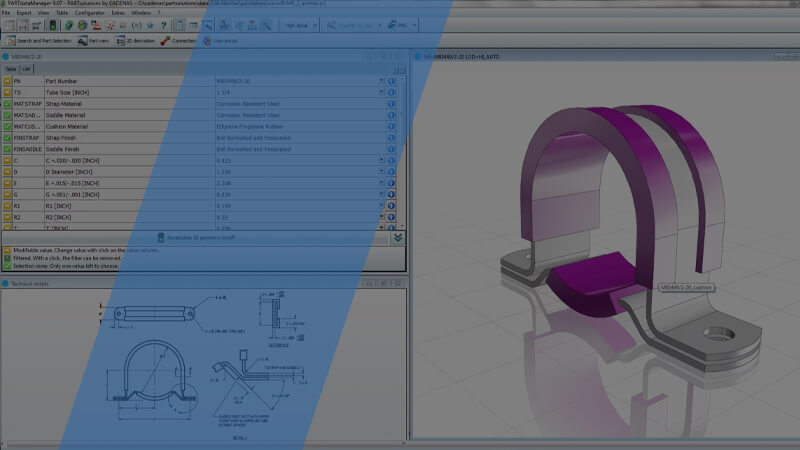
3D design
Components
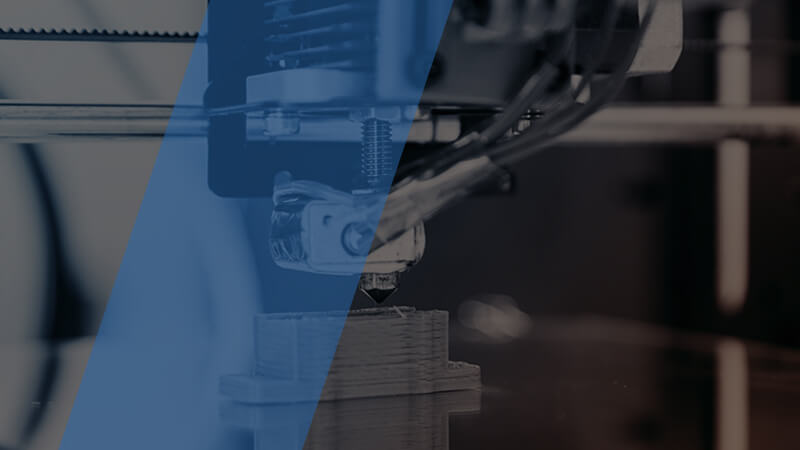
3D printing
Components
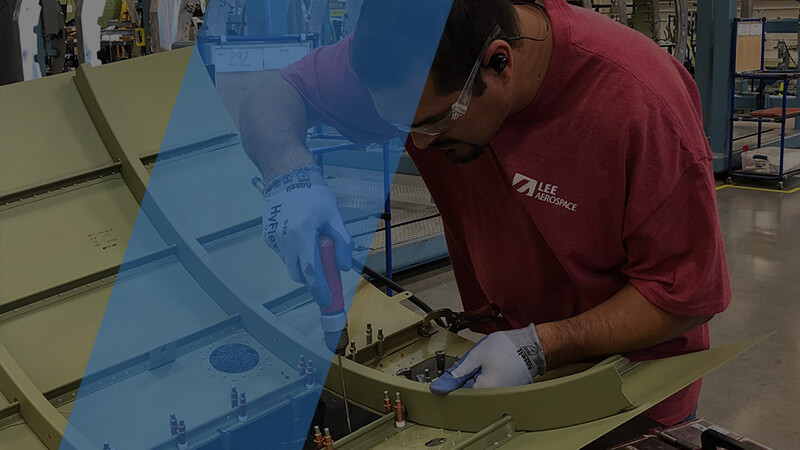
Testing
Components
A range of popular 3D printing materials are suitable for the aerospace industry because of quicker delivery of printed parts. The 3D printer is used to produce high detail and smooth models of aerospace designs.
3D printing is commonplace in the aerospace industry, from a full-size landing gear closure printed rapidly, to a high-detail full-colour control board concept model, there is a 3D printing process suited to every prototyping need.
3D printing aerospace components are quickly printed at a low cost and highly detailed with 3D printers from Dreambot3D.
Production volumes in the aerospace industry are generally large, our 3D printing still proffers the best prototyping solution rather than the manufacturing of end parts. The speed at which our 3D printer prints materials makes it a viable option for medium-sized aerospace printing production.
3D printing aircraft parts requires so much precision and details, these and more is what our printers give you.
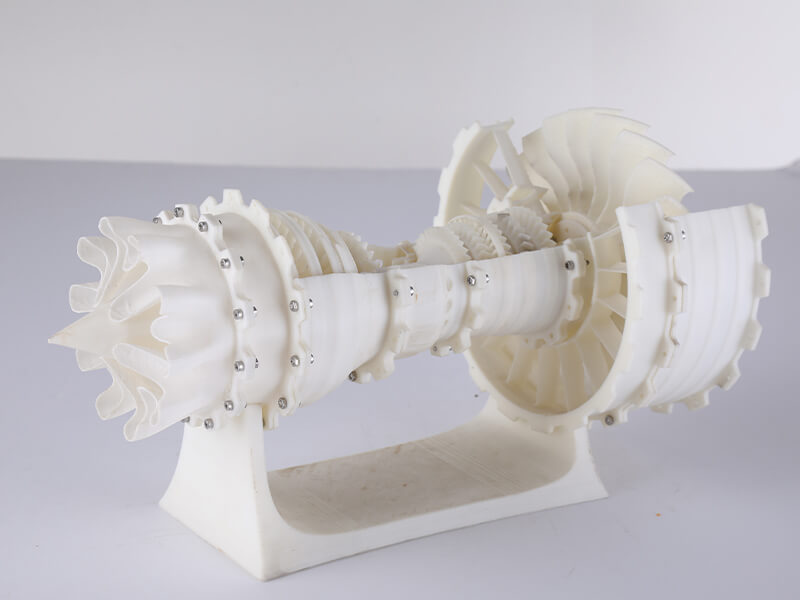
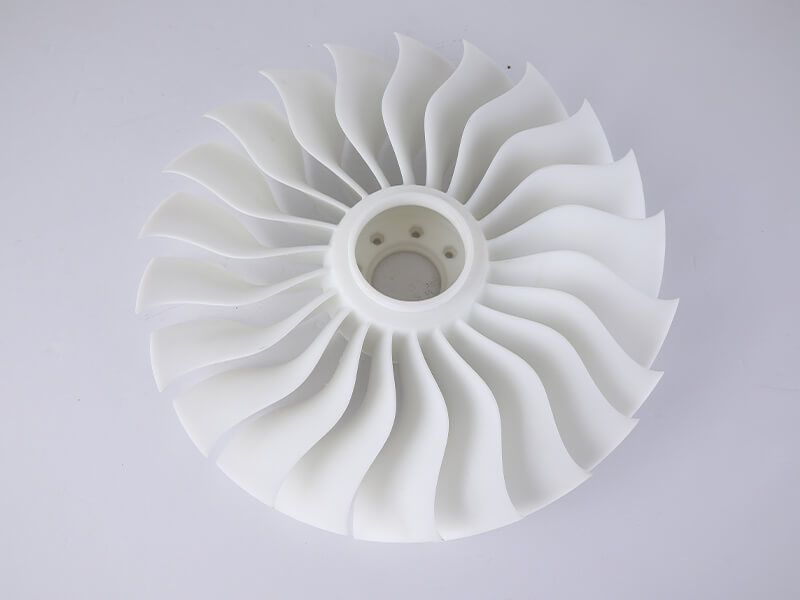
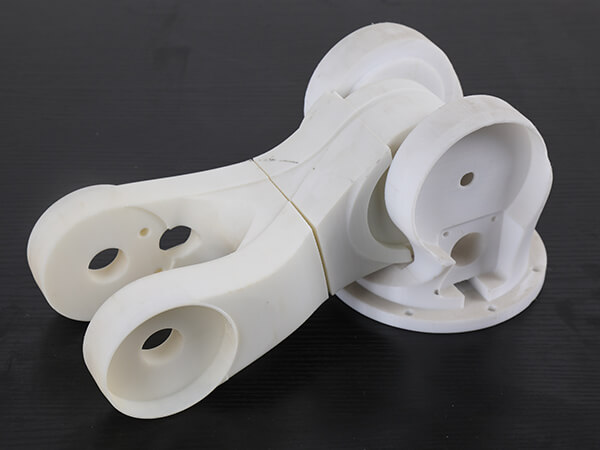
Aerospace 3D printers for your Choice
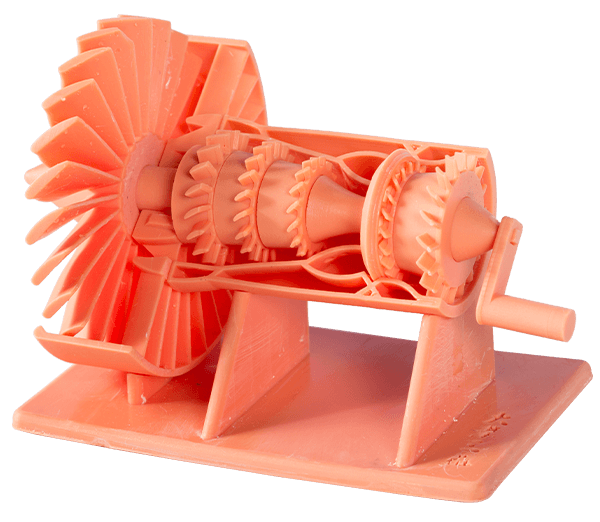
Don't know how to choose a model?
Are you confused about how to choose the correct model and type of 3d printer? We support 24/7.
4 points why choose us
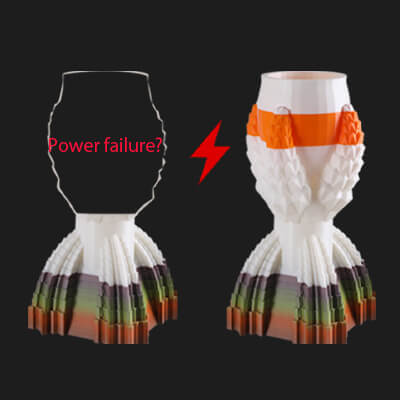
Automatic resume printing
Continue to print the unfinished model after the power is restored when the power fails
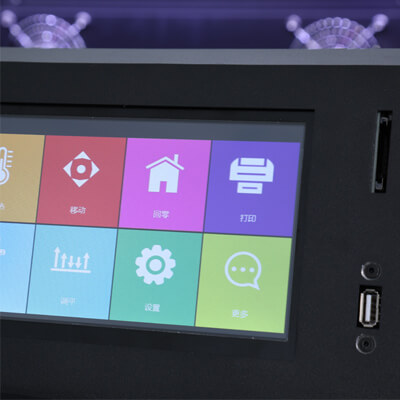
PLC control system
All 3d printers are equipped with PLC control system as standard, makes the operation more convenient, and reduces the error.
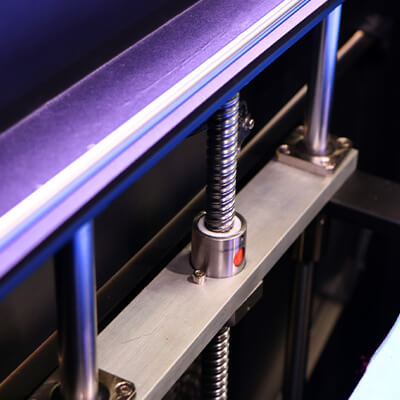
Extremely speed printing
Higher straightness, lower friction coefficient, better smoothness, higher positioning accuracy and more stability during printing.
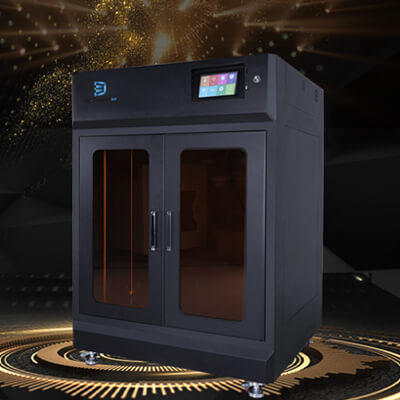
Reinforced structure
The all-metal one-piece shell reduces resonance, makes printing more stable and improves printing accuracy.
What our customers say
How 3D Printers are Used in the Aerospace
Aerospace 3D Printer Buying Guide
Introduction to the original figures production process
One of the first industries to invest in large scale 3D printing was the aerospace industry. Aerospace – the branch of technology and industry concerned with both aviation and space flight – has been evolving and adopting the technology as early as the 1980s.
As commercial air travel has increased, the demand for new aircraft has led to orders of nearly 38,000 new aircraft over the next 20 years. As a result, equipment manufacturers, designers, and suppliers need cost-effective solutions to produce these aircraft as quickly and efficiently as possible.
Like every other industry, the aerospace industry is highly reliant on the productive input 3D printers add to design and manufacturing. 3D printing in aerospace goes beyond the regular spectrum of R&D; its impact has played a major role in the industry’s revolution by reducing weight, strengthening materials, and streamlining design.
Due to the typically short runs of aircraft parts, the aerospace industry uses additive manufacturing for a great deal of its production. The technology can produce intricate parts that are more resilient and lightweight compared to those made using traditional techniques, which is an obvious bonus.
Among the first advocates of 3D printing, the airline industry is a driving force in the evolution of this technology for both manufacturing end-use parts and prototyping. From the impact of 3D printers in aerospace in the life of everyday designers and professionals to its impact on a global scale, the aerospace 3D printer buying process, and frequently asked questions by newbies in the industry, this buying guide covers it all.
1.1, Introduction
The Aerospace industry is a great example of utilization Additive Manufacturing (AM) (commonly referred to as 3D Printing) with a clear value proposition and the ability to create parts that are stronger and lighter than parts made using traditional manufacturing.
The aerospace industry was a very early adopter of 3D printing and still continues to contribute heavily to its development. Some aerospace companies began using this technology as early as 1989, and over the next couple of decades, the adoption of 3D printing increased substantially. In 2015, the Aerospace and defense industry contributed approximately 16% of 3D Printing’s \$4.9+ billion global revenues.
3D printing in aerospace can produce hundreds of thousands of parts without relying on expensive tooling changes involved with traditional manufacturing processes. “Tool-less” production requires less energy since modified parts or upgrades can be produced as needed, alleviating the need for costly storage.
Aerospace parts often include internal channels for conformal cooling, internal features, thin walls, and complex curved surfaces. 3D printing aerospace processes can create highly complex and lightweight structures with high stability whilst allowing for the consolidation of multiple parts into a single component.
This buying guide presents an overview of the use of 3D printing in the aerospace industry. It discusses design requirements for parts used in airplanes and gives design recommendations for common (and not-so-common) aerospace applications. A range of popular 3D printing materials suitable for the aerospace industry is presented along with case studies, where 3D printing has been successfully implemented.
1.2, Common 3D Printer Use Cases in Aerospace
The aerospace industry uses 3D printing to manufacture end-use parts, prototypes, alleviate supply chain constraints, limit warehouse space, cut storage costs, and reduce wasted production materials. Aerospace 3D printing technology is also used to explore ground-breaking innovation by reducing commercial airplane travel emissions, constructing in space, and even bioprinting in space.
3D printers in aerospace cover a wide range of activities. Its usage spans the development, design, and manufacturing process. Thanks to the flexible easy to understand designing sequence 3D printers provide, thousands of professionals and experts in the aerospace industry are enjoying a work experience similar to taking a walk in their favorite park. Let’s take a look at some of the popular use cases of 3D printers in the aerospace industry.
Jigs & Fixtures
Big benefits exist for some of the more mundane 3D printing applications, including jigs and fixture making. For each individual aircraft, companies have hundreds of fixtures, guides, templates, and gauges 3D printed, generally with 60 to 90 percent reductions in cost and lead time compared to other manufacturing processes.
Surrogates
Surrogates are placeholder parts used throughout production that represent components that are later installed in final assemblies. Surrogates are mainly used for training. NASA and several air force bases commonly use surrogate parts on the production floor. Surrogates parts can be designed using aerospace 3D printers.
Mounting brackets
3D printing in aerospace is commonly used to manufacture structural, low-volume metal brackets (with DMSL/SLM) that mount complex lifesaving systems to the interior wall of a plane.
High detail visual prototypes
3D printing with Material Jetting is able to produce multicolor designs with a surface finish comparable to injection molding. These visually appealing models allow designers to get a greater understanding of the form and fit of a part before production decisions.
This highly accurate method of prototyping is also ideal for aerodynamic testing and analysis, as the surface finish that is able to be achieved is often a representative of a final part.
3D printing in aerospace is used routinely to manufacture aerospace components that rely on aesthetics over function, such as door handles and light housings to control wheels and full interior dashboard designs.
As the aerospace industry continues to see the value of 3D printing, we can expect more companies to begin developing on-site 3D printing operations and investing in the technology. Indeed, on-site printing capabilities offer real-time design, processing, trial, and implementation of customized components.
Integrating 3D Printing in the Design Workflow
The aerospace industry includes a range of commercial, industrial, and military applications and is comprised of departments that design, manufacture, operate, and maintain the aircraft or spacecraft. The use of 3D printers in aerospace covers all the phases involved in design and manufacturing.
From design communication, validation stage, pre-production, mass production, and customization—3D printers are involved in all phases. Let’s take a simple yet sophisticated look into how 3D printed airplane parts are obtained at all phase.
2.1, Design Communication
Designs in the aerospace industry often begin as concept models showcasing a component of an aircraft. These are often also regularly used for aerodynamic testing, which is of critical importance for aerospace.
SLA and Material Jetting are used to produce great detail, smooth, scale models of aerospace designs. Accurate models allow design intention to be clearly communicated and showcase the overall form of a concept.
2.2, Validation Stage
Prototyping using 3D printing is now commonplace in the aerospace industry. From a full-size landing gear enclosure printed rapidly with low-cost FDM to a high-detail, full-color control board concept model, there is a 3D printing process suited to every prototyping need. Engineering materials for 3D printing in aerospace also allow for full testing and validation of prototype performance.
2.3, Pre-Production
One of the areas 3D printing in aerospace has been most disruptive and valuable is the production of low-cost rapid tooling for injection molding, thermoforming, and jigs, and fixtures.
Within the aerospace industry, this allows for tooling to be quickly manufactured at a low cost and then used to produce low to medium runs of parts. This plane 3D print validation mitigates the risk when investing in high-cost tooling at the production stage and can also provide production components for quantities up to 5,000 to 10,000 parts.
Note that tooling for injection molded parts in aerospace 3D printing does not need to be made of metal, necessarily. This is particularly important during the pre-production phase when a manufacturer only needs to make a small run of parts for the prototype aircraft or component.
Once the proof of concept has been validated, they can then tweak the design if necessary and then build permanent tooling for the production line.
2.4, Mass Production
Because production volumes in the aerospace industry are generally large (more than 70,000 parts per year), 3D printing in aerospace has predominantly been used in the past as a prototyping solution rather than the manufacturing of end parts. Improvements in the size of industrial printers, the speed they are able to print at, and the materials that are available mean that 3D printed aerospace parts are now viable options for many medium-sized production runs, particularly for high-end interior build-outs.
Prior to production, tooling for injection molding, jigs/fixtures, and thermoforming can be manufactured quickly and at a lower cost thanks to 3D printing in aerospace. While 3D printing in the aerospace industry used to be used for the prototyping phase alone, it is now used more than ever for the manufacturing of end parts, too, since larger industrial printers can print quickly using a variety of materials.
It is important to understand what 3D printing in aerospace is good for and what it is not. It is incredible at transferring a raw file into a finished model and infinite complexity. It is not particularly well suited for mass production.
Each project is time-consuming because it is intended to build intricate designs rather than the rapid production of identical components. This is the reason why it has traditionally been used for rapid prototyping, where parts are a one-off production. As the process and technology continue to improve, though, 3D printers will only continue to increase in speed and efficiency.
2.5, Customization
3D printing technologies have a significant impact on the aerospace industry when the cost of highly complex one-off components can be justified by a substantial improvement in aircraft performance: the average corporate aircraft travel 75,000 miles per month and a single component that was designed and manufactured with 3D printing reduces air drag by 2.1%, reducing fuel costs by 5.41%! Small adjustments like this example affect life in a huge way.
Aircraft parts can be tailored to suit particular government or company requirements thanks to 3D printing, whether it’s a specific cabin interior design or functionality tailored towards the unique purpose of a particular aircraft e.g., cargo plane, passenger aircraft, or helicopter.3D printing in aerospace also provides part consolidation and topology optimization of many custom aerospace components.
The Benefits of 3D Printing for Aerospace
3.1, Low-volume production
The great thing about 3D printing is its ability to be adapted to basically anything which the filaments available can create. It can make three-dimensional shapes of any level of complexity imaginable, making it an ideal solution for rapid prototyping for a number of markets, notably aerospace, defense, and the automobile industries.
It is reasonable to surmise 3D printing in aerospace as a viable prototyping method for a number of components for ground support equipment prototypes. It can be used to build full-scale mock-ups of sun drives, gear reductions, and even circuit boards; any assembly or sub-assembly mock-up can be easily built to exacting specifications.
3D printing in aerospace enables engineers to prototype and validate conceptual design faster. Since tooling production can be skipped to go straight to finished parts, it speeds up the overall development process. The ability to prototype without tooling enables companies to quickly test multiple configurations in order to determine customer preferences and reduce product-launch risk and time to market.
Likewise, 3D printed airplane parts are advantageous for demonstration units and short-volume production where it brings down or eliminates the cost for expensive and poorly amortized manufacturing tooling.
3D-printing in aerospace goes well along with crowd-sourcing ideas through remote cooperation, which, over time, will likely affect how companies manage R&D. That crowd-sourced brainpower might someday supplant traditional R&D, making its management a new priority.
3.2, Weight Reduction
Weight is a key driver for airlines because lighter aircraft have double the impact on the industry. Lighter weight leads to lower fuel consumption (and CO2 emissions) and to the competitive advantage of reduced costs and better airfares.
Space vehicles also require intricately designed parts to minimize packaging space and reduce weight. Such parts are typically produced in very small volumes, and if traditionally manufactured, they are expensive and time-consuming.
3D printers undoubtedly help reduce the weight of aerospace components by printing more efficient geometries, topologically optimized, and lattice structures that carve out significant amounts of unnecessary material.
3D printing in aerospace allows for a single, large component to be built from the ground up in a single unit rather than a lot of small parts being assembled for a single component. In doing so, it will allow manufacturers to reduce material waste, weight, and bulk.
Note that traditional manufacturing methods, such as milling, often lead to the production of significant amounts of waste material. Yet, 3D printing in aerospace uses less energy and is able to significantly reduce the amount of waste produced based on its method of developing parts layer by layer. The benefit here is that materials are being used more effectively and efficiently, helping you to save money on purchasing materials.
3.3, Material Efficiency
3D printing in aerospace challenges the traditional dilemma between scale and scope that prevails in manufacturing in two ways. First, it reduces the capital required to achieve economies of scale. A single printer can simultaneously build several complex parts with variable designs.
Therefore, large centralized factories with assembly lines are no longer required. Second, 3D printers in aerospace increase the variety of designs that an amount of capital produces. Hence, complexity, production changeovers, and customization are cheaper.
Some aerospace parts are made of expensive materials such as titanium Ti6Al4V or super-alloy Inconel 718. Such raw materials are traditionally hard to shape when long machining is required.
Depending on the geometry, production without the use of 3D printers in aerospace can involve a high amount of material waste, resulting in a costly loss and the need to undertake recycling operations.
While raw powder materials for metal 3D printing are expensive, the process of 3D printing in aerospace creates far less material waste. 3D printing in aerospace offers solutions that allow exact replicas of structural components to be printed on an as-needed basis.
Since this type of repair does not require extensive tooling and die production, the turnaround time will be absolutely unheard of. It could be measured in hours or days rather than weeks.
With 3D printing in aerospace, designers are able to produce highly complex designs that can be produced into a single part, avoiding the need to produce and assemble a series of smaller parts.
This can also be achieved by using 3D printing in the production of tooling. Using 3D printing in aerospace for fabrication allows you to create complex tooling designs that can be used to create more customized end products. And with less waste produced, the entire process is more cost-efficient compared to traditional manufacturing.
3.4, Part Consolidation
3D printing in aerospace is an excellent application of additive manufacturing for the A&D industries. Consider the extensive process involved in creating dies for a trial modification on a given component.
Using plane 3D prints, an exact replica can be made of a non-certified polymer, which offers all of the fit and finish of the final project for the sake of a non-functioning mockup at a tiny fraction of the price. More importantly, it gets a scale model of the product on the showroom floor incredibly fast.
As a consequence of the high design complexity possible, 3D printing in aerospace offers the ability to consolidate multiple parts into fewer components, directly reducing the assembly time and costs. Moreover, it simplifies eventual design modifications.
In theory, consolidating a design reduces the need for joining several parts together by welding or any other method that potentially impairs reliability and durability.
Design strongly depends on which manufacturing techniques are employed. Engineers traditionally design anything by considering the possibilities and limitations of milling, turning, casting, forging, and welding. Traditionally, some designs optimized for topology are not producible due to their complex shapes.
3D printed aerospace parts can fabricate complex components out of a variety of plastics and metals, such as steel, aluminum. Aerospace already benefits from 3D printed Titanium Ti6Al4V and Inconel 718, which offers superior flexibility in terms of feasible geometries and creates more space to innovate and explore new designs. It also allows designers to better serve maximum performance without the need to accommodate manufacturing limitations.
3.5, Maintenance & Repair
Maintenance teams are always under pressure to deliver service quickly, efficiently, and at low cost. The major task of maintenance is to decrease unplanned downtime and, therefore, increase Overall Equipment Effectiveness (OEE). 3D printing in aerospace helps maintenance in reducing downtime by increasing the availability of replacement parts or repair fixtures – in many cases at a lower cost and with faster turnaround time.
For experts in the aerospace industry, producing spare parts and tools faster means increased machine uptime and fewer production disruptions. For consumers, it means less waiting time for someone to repair a car or appliance. Note that if a jet plane or aero part is maintained properly, assets can operate for many years. But inevitably, jet plane parts will become outdated and spare parts may be difficult to find or too expensive to order.
Take the railway industry as an example. The service life of trains typically ranges between 35 to 45 years. Train operators are therefore faced with several challenges when it comes to vehicle maintenance and replacement for older train parts, which can be difficult to source.
One such challenge is the downtime cost per day for a train, which can be quite high. It’s estimated that a train part in need of replacement, which costs less than €100, can often set back a single major U.S. commuter rail service €18,000 for every day that the part keeps a train out of service.
In order to cope with such challenges, companies – not only in the railway industry but also in other sectors, where assets typically serve for many years, like aerospace and oil and gas – seek new ways of producing obsolete spare parts faster and more economically.
3D printing is becoming one of the technologies that can solve such issues. It’s a digital manufacturing technology, which means that it relies on digital workflows and doesn’t require additional tools, like molds, to create a part.
Without the need for such tools, 3D printing in aerospace can cut the manufacturing time significantly for obsolete spare parts, in some cases by as much as 95 percent. The process is also frequently coupled with reverse engineering, particularly when the original design of a part has been lost.
3D Printing Materials for Aerospace Application
3D printing has enabled aerospace companies to create complex components previously impossible with traditional techniques. This fosters innovation while reducing costs and turnaround times in a complex, highly-regulated environment.
Due to the typically short runs of parts, the aerospace industry is a prime candidate to benefit from 3D printing. 3D printing in aerospace gives companies the flexibility to print specific aerospace parts for applications in the hundreds or thousands without costly tooling changes.
Beyond part production, 3D printing aircraft parts improves manufacturing capabilities for tools that are needed to create those parts. It can also facilitate light-weighting efforts for aerospace structures, increasing fuel savings, and reducing environmental impact.
Unlike in most other industries, you can use a filament or resin 3D printer for 3D printing material in aerospace. While filament runs dominant in the industry, the use of resins is on the rise. So, whether you use an SLA, LCD, DLP, or FDM 3D printers, you can 3D print aircraft parts; rest assured the superior finish you desire is guaranteed.
Before we dive into the various 3D printers widely used in the aerospace industry, let’s take a look at the types of materials suitable for creating aircraft parts in the aerospace industry.
4.1, ABS {Acrylonitrile Butadiene Styrene}
As a thermoplastic polymer, it can melt and cool without altering its chemical properties. That makes it an interesting industrial FDM 3D printer material for 3D printing in aerospace. The filament is known to be strong, tough, and durable. It is also forgiving to scratches, offers good resistance to heat and everyday chemicals.
It can endure heat, pressure, and stress like no other industrial FDM material for airplane 3D printing, making it a great choice for wear and tear prints. You can try this out yourself: If you move a strain of ABS filament, it will distort and bend before breaking. PLA breaks much more easily.
ABS is quite forgiving, as long as you print with the right settings and proper temperature management. You can even achieve overhangs of around 45 degrees. If the print succeeds, the results are very convincing.
Most makers like the material because you can process its surfaces with acetone, glue parts, and even file off some material. Lastly, it can be easily painted with acrylic colors. ABS filament is not toxic when 3D printed. Only at very high temperatures (400 °C), the material decomposes into butadiene (which is carcinogenic to humans), acrylonitrile (possibly carcinogenic to humans), and styrene—nothing you want to inhale under any circumstances.
If you don’t have an airplane 3D printer at hand, you can have ABS parts printed by a professional 3D printing service. You can put a call through to our support representative to obtain the best deal on a high-resolution FDM 3D printer for aerospace 3D printing.
4.2, PLA {Polylactic Acid}
PLA filament is by far the most popular industrial FDM 3D printer material used for 3D printing in aerospace, and there’s a good reason for that. It comes in many shades and styles, making it ideal for a wide range of applications. Whether you’re looking for vibrant colors or unique blends, it’s an easy-to-use and aesthetically pleasing material.
PLA is short for Polylactic Acid, a thermoplastic polymer that is derived from renewable resources, more specifically from corn starch or sugar cane. This sets the material apart from other commonly used plastics, which are procured through the distillation and polymerization of non-renewable petroleum reserves.
Since PLA filament is a biodegradable product, it tends to naturally break down in about three to six months. Other thermoplastic materials can take up to a thousand years to decompose, making PLA much more environmentally-friendly.
PLA material has been thrust into the spotlight by the rise of custom industrial FDM printers. PLA filament is available in a wide variety of colors and blends, and innovative PLA-based materials seem to be constantly hitting the market.
Outside of aerospace 3D printing, PLA is also used to produce things like medical implants, food packaging, and disposable tableware. But inside of the industrial FDM 3D printing sphere, PLA filament is widely thought of as an aesthetic material best used for prototyping.
4.3, Nylon
Nylon (a.k.a. Polyamide) is a popular material in the aerospace industry, known for its toughness and flexibility. Nylon filaments typically require extruder temperatures near 250 ºC. However, some 3D printers in aerospace allow printing at temperatures as low as 220 ºC due to their chemical composition.
Many airplane 3D printers do not include a hotend that can safely reach 250 ºC, so these lower-temperature versions can be useful and potentially save you from needing to upgrade your hotend. One big challenge with Nylon filaments is that they are hygroscopic, which means they readily absorb moisture from their surroundings.
Printing Nylon after it has absorbed moisture will lead to several print quality issues; thus, filament storage becomes very important and requires special attention. Some of the Pros of using Nylon filament on your custom FDM printer include;
- Tough and partially flexible
- High impact resistance
- No unpleasant odor while printing
- Good abrasion resistance
Cons of Nylon Filament
- Prone to Warping
- Air-tight storage required to prevent water absorption
- Improperly dried filaments can cause printing defects.
4.4, Resin
While FDM 3D printing technology uses traditional industrial plastics like ABS and Polycarbonate (PC), SLA, DLP, and LCD 3D printers require special photopolymer resins that harden (cure) once UV light is directed at it. Most 3D printing resins are either epoxy-based or acrylate-based, the latter being used more often in desktop printers.
A lot of people think of resin 3D printed parts as fragile and most suitable for ornamental and prototyping applications rather than functional and load-bearing components. But this is only true if the resin isn’t properly selected. That being said, if you’re buying a generic resin for a tough job, it won’t give you the strength that you’re looking for.
Examples of super-strong resin can be found in a wide variety of industries. There are castable resins for making jewelry and 3D printing in the field of dentistry to produce mouth guards, crowns, and surgical guides. There’s also high-temperature resins that are suitable for 3D printing in aerospace and even resins that can produce rubber-like parts.
As the definition suggests, tensile strength values are usually measured by a pull test that follows strict international procedures, so the results can be used worldwide. The higher the tensile strength, the stronger the material is considered to be because of how much stress it can withstand.
Just because the resin is tough, it doesn’t mean that the 3D printed aerospace part made from these resins will be twice as strong as if printed with a standard resin. Other factors, like model design and print settings, play important roles in the final print’s strength, which we’ll discuss in more detail later.
Nonetheless, comparing tensile strength is a straightforward way to determine which material is stronger, and from the numbers supplied by the manufacturers, it’s clear that these resins are much tougher than the standard.
How to Choose a 3D Printer for Aerospace
A few years ago, just being able to utilize 3D printing in aerospace manufacturing was enough of a competitive edge. Companies quietly qualified materials and processes and utilized these technologies to gap their competition in platform capability, weight, or reduced payload volume.
Today, the materials focus is growing from just plastics to include a metallic material, paving the way for new opportunities. When materials such as additive manufactured metals gain a strong foothold, we’ll see use cases increase dramatically within the defense, aerospace, and space industry.
In this section, we would be focusing on all the information you need to choose a 3D printer for the aerospace industry. Before we dive into the steps and processes involved in choosing a 3D printer for your aerospace printing line, let’s look at the types of printers that can be used and the working principle behind their day to day operations.
5.1, Which Machines are Needed and for What Purpose
LCD, DLP, SLA, and FDM 3D printers are all durable printing machines for individuals looking to enjoy the lucrative edge 3D printing brings to the aerospace industry. However, some professionals would fancy the flexibility of LCD over FDM, while other experts might fancy DLP over SLA. To help you pinpoint the right 3D printer for your aerospace 3D printing line, let’s look at the working principles behind the aerospace 3D printers available.
5.1.1 3D Printer
Fused Deposition Modelling {FDM}
FDM industrial 3D printer is currently the most popular aerospace 3D printing technology. It is used in both affordable 3D printers and even 3D pens. F
DM printing was originally developed and implemented by Scott Crump from Stratasys, founded in the 1980s. Other 3D printing companies have embraced similar technology but under different names. A well-known manufacturer MakerBot coined a virtually identical technology, calling it Fused Filament Fabrication (FFF).
Airplane 3D printers that use FDM Technology construct objects layer by layer from the very bottom up by heating and extruding thermoplastic filament. The whole process is somewhat similar to stereolithography. Specialized programs or Slicers “cut” CAD models into layers and computes the manner printer’s extruder would assemble each layer.
In addition to thermoplastic, a printer may extrude support materials too. Then the printer heats thermoplastic until its melting point and extrudes it throughout the nozzle on a printing bed, which you may know as a build platform or a desk, on a predetermined pattern determined by the 3D model and Slicer software.
The Slicer software running on the computer connected to the aerospace 3D printer translates the measurements of an object into X, Y, and Z coordinates and controls the nozzle and the foundation to follow the calculated route during printing.
When the thin layer of plastic binds to the layer beneath it, it melts and hardens. When the layer is completed, the base is lowered to accommodate the printing of the next layer.
Liquid Crystal Display {LCD}
Liquid crystal display printers or LCD printers as they are popularly known are industrial 3D printers use to create 3D models or designs of numerous objects in education, automotive, aerospace, medicine, dentistry, etc. LCD printers generate their light source through an array of UV LCDs.
These printers are used to create 3D patterns or images of CAD models using materials such as resin, wax, or metals. The images or 3D models obtained using LCD 3D printers are composed of dots.
LCD aerospace 3D printers display images by sending light from a metal-halide lamp through a prism or series of dichroic filters. This dichroic filter separates light into three polysilicon panels. In simple terms, an aerospace LCD 3D printer uses an array of UV LCD as its light source. The printer shines light directly from the flat LCD panel in a parallel fashion onto the build area.
As the light travels through the light source, the individual pixels open up to allow light to pass or close to block the light. This combination of open and closed pixels creates room for the liquid polymer 3D printer to produce multiple colors and shades on the projected image.
The light emitted from an LCD aerospace 3D printer isn’t expanded—that’s, it doesn’t spread beyond its projected frame. When using these 3D printers, you can design patterns and images of multiple variations; rest assured you wouldn’t experience pixel distortion halfway. Note that unlike most other resin printers, the LCD aerospace 3D printers print quality depends on its LCD density.
Digital light processing {DLP}
DLP is another aerospace 3D printer quite much like stereolithography. The DLP technology was made in 1987 by Larry Hornbeck of Texas Instruments and became well known for its use in the production of projectors.
It utilizes digital micromirrors laid out on a semiconductor chip. The technology is found in mobile phones, film projectors, and, of course, in aerospace 3D printing. For 3D printing, both DLP and SLA functions with photopolymers. However, the difference between SLA and DLP industrial 3D printers is that DLA requires an additional source of lighting.
3D printing amateurs frequently use more traditional sources of lights like arc lamps for DLP printing. The other important piece of the DLP puzzle is an LCD (liquid crystal display) panel, which gets applied to the entire surface of the 3D printed layer during a single run of the DLP procedure.
The substance used for printing is a liquid plastic resin that’s set in a transparent resin container. The resin hardens quickly when exposed to a lot of photons, or more simply put, bright light.
The printing speed for DLP industrial 3D printers is the kicker. A layer of hardened material can be produced with this kind of printer in a few seconds. After the layer is completed, it is transferred, and printing of the next layer is started.
Stereolithography SLA
SLA is an aerospace 3D printer that could be used to execute your projects that involve the 3D printing of items. Although this process is the earliest one in the history of 3D printing, it is still in use today.
The idea and application of this method are amazing. Whether you’re a mechanical engineer, who wants to confirm whether the part can fit your design or a creative individual who wishes to print a plastic prototype for a fresh upcoming project, Stereolithography 3D printing systems can truly bring your 3D models to life.
SLA aerospace 3D printers do not function like normal desktop printers that extrude some quantity of ink to the surface. SLA 3D printers operate with an excess of liquid plastic that, after a while, hardens and forms to a solid object. Note that parts printed by stereolithography 3D printers usually have smooth surfaces, but their quality depends on the quality of the SLA printer used.
After the plastic hardens, a stage of the printer drops down in the tank, a fraction of a millimeter, and laser forms another layer until printing is finished. After all, layers are printed, the item has to be rinsed using a solvent and then put in an ultraviolet oven to complete processing.
The time required to print an object depends upon the size of the SLA aerospace 3d printing system utilized. Small items can be printed within 6-8 hours using a basic kid’s 3D printer, while large 3d prints can be several meters in 3 dimensions, and printing time could be up to several days long.
5.1.2 3D Scanner
3D scanning is the process of analyzing a real-world object or environment to collect data on its shape and possibly its appearance (e.g., color). The collected data can then be used to construct digital 3D models. A 3D scanner can take almost anything and digitize it.
Using special software and a scanner, an object can be “captured” as a digital image by taking measurements from light bouncing off of the object.
Experts in aerospace 3D printing have the ability to capture and manipulate physical objects and bring them into the digital world. In many cases, it can eliminate lengthy and costly design and development processes.
Since 3D laser scanning services can replicate just about anything, there is a lot that can be done with it for 3D printed airplane parts. You could take any part of your airplane and have it scanned. From there, a 3D printer could reproduce it using a specific material that you want. It could be plastic or metal.
5.2, How to Choose the 3D Printer
Now to the part we have all been waiting for—the choosing process. In the aerospace industry, the type of 3D printer you purchase says a lot about the durability and efficiency of your printing line/R&D team. If you want to enjoy maximal production at minimal cost, we recommend you take out time to explore the factors discussed below.
Spending time to understand all the intricacies attached to purchasing a 3D printer before settling for any manufacturer or brand would provide you with an edge in the buying/decision-making process. Below are the major factors you need to keep in mind when making your aerospace 3D printer buying decision.
5.2.1 What is the size of the Print
Aerospace 3D printers come in multiple variants. Some are suitable for large printing tasks, while others possess printing jet plane parts that can cater to only small tasks.
How big is your aerospace 3D printing project, and what size of prints do your customers demand from you regularly? At Dreambot3D, we have seen the irregularities and extra expenses that come with purchasing an industrial FDM 3D printer or LCD 3D printer that’s not compatible with the print size.
Over the years we have been in business, we have had the opportunity of interacting with consumers from different countries and regions. One of the most highly influential factors most hobbyists or professionals who have walked through our door to purchase an airplane 3D printer ignore is the size of the print.
Yeah, it’s practically impossible to determine the exact size or specification attributed, or that would be required in most of the prints you make—especially if you are a business owner looking to satisfy the needs of clients from different parts of the world. However, totally ignoring the print size of your industrial FDM 3D printer or an LCD 3D printer can create is unacceptable.
FDM 3D printers garnered renowned usage ahead of LCD, SLA, and DLP as a reputable aerospace 3D printer not just because of its printing speed or the remarkable finish product it is known for, but also because of its ability to perfectly create sustainable 3D models using filaments.
Before buying any LCD, SLA, DLP, FDM industrial 3D printer, try to know the type of filament it can print on and whether it’s durable enough to print perfect models on wide materials without leaving distorted edges.
The material you chose for your printing task has a lot to say about the printing size. The dimension, weight, and size of the object obtained from a 3D model printed with PLA are quite different from the result you would obtain using an ABS material—regardless of whether the CAD file and design are the same. Considering the type of materials you would print on regularly can help you pinpoint an aerospace 3D printer that wouldn’t create constraints in your design’s dimension, weight, and size.
5.2.2 Choose a Reliable Brand
Hundreds of brands have built a formidable reputation for themselves by offering aerospace 3D printers with remarkable features. While it’s essential you check out a brand’s track record and reviews from previous customers, it’s also important you don’t base your buying decision entirely on a brand’s name.
There are a lot of industrial aerospace 3D printers available world-wide with reputable brand tags but void of the innovative design and features required to keep your printing line functional. Many brands built a good name for themselves in the early 90s but haven’t been able to keep up with the diverse changes needed to excel in the 21st-century market.
Before putting hours of research into exploring a brand’s portfolio or track record in the global market, make sure the airplane 3D printer you want to buy possesses features in line with your needs and has been ascertained satisfactory by other users and experts in your industry.
There are so many aerospace 3D printers being developed and released into the market every day. While most of these printers meet the basic requirements and features of SLA, FDM, LCD, SLS, DLP printers, you should not be hasty while sealing the deal yet. Why? You may ask.
3D printers are not cheap machines. You’ll part ways with a considerable amount of your money; therefore, you must ensure that you get value for your money. While your choice should not solely be made on the brands’ name, it is crucial that you do thorough background research on the company’s Google ratings and reviews before making a purchase.
Consider buying your printer from an industrial aerospace 3D printer manufacturer that has a good track record, a higher rating on Google, and a genuine customer support system. Such a company will be apt to respond to all your urgent needs, for instance, if your printer breaks or runs out of filaments. The company/brand that you’ll pick for your printer can make or break your printing experience if something goes amiss.
5.2.3 Safety Configuration of the Machine
When purchasing or using an aerospace 3D printer, you must keep in mind that safety is paramount. And this is not just because you wouldn’t want to expose yourself to the toxic fumes most airplane 3D printers emit during the design and creation process, but also because your ability to build a lucrative 3D printing business is largely dependent on how safe and ready-to-use your aerospace 3D printers are.
If this is the first time you are tasked with handling all the challenges that come with purchasing an airplane 3D printer, the safety configuration of the machine might seem alien to you. Don’t neglect the durability effect that comes with purchasing an aerospace 3D printer with safety configurations that does not reflect the productive ability of the machine.
When making your 3d printing machine buying decision, you need to be on the safe edge. The only way to achieve this feat is by putting due diligence into every step involved in the process. Note that the safety configuration of most aerospace 3D printers is quite complex and bulky. To demystify this tiring yet important process, consult with a support service representative before finalizing your buying decision.
5.2.4 Resolution Requirement of the Machine
3D printing resolution is the level of detail quality at which your part is created. Aerospace 3D printers extrude plastic through a nozzle to create 3D printed objects. That nozzle pin can be adjusted to different widths to allow for higher or lower resolution printing. It’s necessary that you keenly take into account the resolution of a printing machine before buying one, depending on the industry you are operating in.
While the resolution requirement of an aerospace 3D printer is regarded as the number one factor to consider when making a 3D printer purchase by experts in numerous industries, this can be referred to as a myth that doesn’t apply to all. The resolution of an FDM or LCD 3D printer determines the clarity and precision that can be enjoyed from a given 3D model and pattern.
However, the resolution of a 3D printing system used in the animation industry doesn’t have to be on the same level as the one used in the aerospace industry. When looking at the resolution requirement of an industrial FDM 3D printer, it’s important you take into consideration the industry you are operating in. In which industry do you want to use the machine? What sort of models do you want to print? How clear or precise does the model have to be for it to be termed efficient?
Answering the above-listed questions would help you demystify some of the myths attached to buying a 3D printer. Yeah, buying a high-resolution aerospace 3D printer should be considered a priority if the funds and budget to finance it is available. But in scenarios where you are on a budget, you can save cost by analyzing the machine usage and model requirement.
Airplane 3D printers come in different variants, shapes, and sizes, optimized with a fitting design and resolution. At Dreambot3D, our daily task revolves around catering to individuals’ dynamic needs and desires from numerous parts of the globe. We know how daunting navigating a machine with a proper resolution can be.
Dreambot3D core value is to provide satisfactory all-round services. To keep up with this mission, we offer a support team that can help you understand the resolution requirements of multiple machines, the industries they are optimized to serve and direct you towards multiple variants that would serve you better.
Note that while the quality of print detail is more paramount in some industries than it is in others, the resolution of a machine decides how fine the details of your part will be. A lower resolution, less quality, and low details on the print object. The objects will have smooth surfaces at the expense of extra filament usage and time consumption. A high resolution, conversely, gives fine quality and better details on print objects.
5.2.5 Consider Weather the Price of the Machine is Acceptable
It’s never a fun experience to have explored all the remarkable features and benefits an aerospace 3D printer is offering, weighed it with your production line, and obtained satisfactory results just to find out during checkout that the aerospace 3D printer you want to purchase is far above your budget.
Airplane 3D printers are quite expensive. They require a sizable investment, especially if you are looking for industrial-grade printers. As a professional or expert looking to help individuals from different walks of life obtain the jet plane parts design or finish product they desire, having the best aerospace 3D printer is essential.
Before exploring all the features and benefits of an airplane 3D printer, weigh its price range with your budget. Note that the price of an aerospace 3D printer does not determine efficiency. There are a lot of aerospace 3D printers with a high price but not as durable and efficient as counterparts with low price tags.
To hasten your 3D printer buying process in terms of price, it’s advisable you put a call through to a support representative backing up the activities of a brand of choice stating your estimated budget and the type of 3D printing activities you would like to carry out using the machine.
5.2.6 Consider the Suppliers After Sales Service Capability
LCD and FDM airplane 3D printers are quite expensive. A good aerospace 3D printer requires an investment well above a thousand dollars. Budget and pricing is a basic factor that must be considered before you kickstart the buying process.
While most of the renowned printing systems available are quite expensive, don’t make the mistake of basing the efficiency or durability of a commercial-grade 3D printer on the price tags attached. There are lots of LCD and FDM 3D printers offering high-quality printing services at cost-efficient rates.
If you run a big production line or you are a hobbyist looking to purchase a remarkable 3D airplane 3D printer, and you firmly stand by the belief that your budget is sizable enough to purchase any printing machine of choice—we recommend you explore our catalog armed with the basic features and specification you require from a preferred FDM or LCD 3D printer.
On the other end, if you are on a low budget and require something substantial to cater to your day to day printing needs, please put a call through today—our support representative will guide you through the buying process.
Sometimes people tend to purchase airplane 3D printers based on the price only. The price of an aerospace 3D printing machine plays a big role in the decision-making process. But with so many industrial and commercial aerospace 3D printers available for sale at the consumer level today, you must keep a keen eye on the machine’s brand, resolution, and safety configuration.
5.2.7 Consider the Service Life of the Machine
The service life for most airplane 3D printers is about 5 to 10 years. While the warranty policy on most 3D printers doesn’t grant you access to refunds or after-sales privileges 1 or 2 years after purchase, purchasing a 3D printer for the aerospace industry from a reliable manufacturer comes with the guarantee that your airplane 3D printer will be in shape and keep your production line running for at least five years.
With that being said, it’s important to note that the estimated service life of the machine can change at any time based on external factors. How you use your machine determines how long it would last. If you leave your industrial FDM 3D printer or LCD 3D printer packed dirty on a regular, you shouldn’t expect the ten years life expectancy to hold any ground.
If you went gone through the hassle of finding the right aerospace 3D printer manufacturer, inspecting all the necessary features, and finalizing the purchase, you wouldn’t want the whole effort you put in to go down the drain based on negligence on your part. Try as much as possible to keep your aerospace 3D printer clean and in good shape, and service life expectancy wouldn’t be an issue.
5.2.8 Consider the Maintenance Cost of the Machine
Using airplane 3D printers to print for hours can cause some mechanical parts to lose their grip or hold to the machine; some might degrade after months of being used. If not upgraded, the final quality of your prints will consequently reduce.
Machine maintenance is necessary, and it might come with added costs where some parts like the nozzle may need to be replaced entirely. You must incur a reasonable maintenance cost of your machine to consistently get clean and fine detailed prints.
Dreambot3D is a 3D printer manufacturer that defied the odds by manufacturing aerospace 3D printers that are highly versatile, cost-effective, easy to use and maintain while still giving you high detail prints. If you are interested in finding out which aerospace 3D printing equipment is best suited for your needs, get in touch with our support team today.
Conclusion
The aerospace industry is one of the earliest adopters of 3D printing, with the first use of the technology going back to 1989. Now, three decades later, the aerospace industry represents a 16.8% share of the $10.4 billion additive manufacturing markets and heavily contributes to ongoing research efforts within the industry.
3D printing aircraft part is a complex job that requires the best aerosapce3D printer. With lots of manufacturers priding themselves as the number one supplier of top-notch airplane 3D printers with long-lasting service life and a smooth and efficient surface finish, it’s almost impossible to accurately pinpoint suppliers/manufacturers that can actually provide such solutions.
Dreambot3D is a 3D printer manufacturer dealing in the manufacturing and distribution of airplane 3D printers. We have been in operation for decades and have built a sustainable track record that speaks for us. Most experts and professionals in the aerospace 3D printing industry regard our supply line as a one-stop catalog for all things 3D printers.
If you would like to have a first-hand overview of our services, how we manage to build such reputable credibility across multiple industries, or better still, equip your aerospace printing line with exceptional 3D machines, put a call through to our support team today—we are available on around the clock basis.
FAQ Guide
How is 3D Printing Used in Aerospace?
The aerospace industry uses 3D printing to manufacture end-use parts, prototypes, alleviate supply chain constraints, limit warehouse space, cut storage costs, and reduce wasted production materials. It is also using the technology to explore groundbreaking innovation via reducing commercial airplane travel emissions, constructing in space, and even bioprinting in space. As the aerospace industry continues to see the value of 3D printing, we can expect more companies to begin developing on-site 3D printing operations and investing in the technology. Indeed, on-site printing capabilities offer real-time design, processing, trial, and implementation of customized components.
How is 3D printing transforming the aerospace industry?
The widespread adoption of 3D printing is most visible in the aerospace and automotive industries. These were some of the first industries to adopt 3D printing for end-use parts in the first place, and so they have the most accumulated experience. The ability for additive technologies to produce single, lightweight pieces with complex internal geometries is particularly valuable for these industries.
What is 3D printing in the aerospace industry?
3D printing enables to build objects with less material, are lighter, and reduces the environmental footprint of the manufacturing process. Thus, 3D printing highly suits the aerospace industry, which pursues improvement in aircraft efficiency, fuel savings, and reduction in air pollution. 3D Printing, also known as Additive Manufacturing (AM), is a process whereby a real object of virtually any shape can be created layer by layer from a Computer-Aided Design (CAD) model. 3D printing is opposite to the conventional manufacturing methods (e.g., extrusion and injection molding) in which the objects are molded into specific forms or cut and formed from a block of material. As opposed to the conventional ‘Subtractive Manufacturing’ that uses cutting, drilling, milling, welding, etc., 3D printing is a free-form fabrication process and does not necessarily require any of these processes.
How is 3D printing used in aerospace manufacturing?
3D printing is used routinely to manufacture aerospace components that rely on aesthetics over function, such as door handles and light housings to control wheels and full interior dashboard designs. One of the areas aerospace 3D printing has been most disruptive and valuable is the production of low-cost rapid tooling for injection molding, thermoforming, and jigs, and fixtures.
What are the three steps of the 3D printing process?
- Step 1: Print
- Step 2: Wash
- Step 3: Sintering
Can I 3D print aerospace parts?
Yes, you can 3D print aerospace parts. The Aerospace industry is a great example of utilization Additive Manufacturing (AM) (commonly referred to as 3D Printing) with a clear value proposition and the ability to create parts that are stronger and lighter than parts made using traditional manufacturing. The aerospace industry was a very early adopter of 3D printing and still continues to contribute heavily to its development. Some aerospace companies began using this technology as early as 1989, and over the next couple of decades, the adoption of 3D printing increased substantially.
How long do 3D printed parts last?
They’ll last effectively forever. The only situation where degradation would maybe be a concern is if you were planning on putting your resin or filament parts outside on the ground, and even then, it would take months or years. We smashed some filament parts outside a year ago and didn’t bother to clean them up, thinking they might biodegrade, but the pieces are still there, just as we left them. The real reason you’re supposed to keep filaments and resins in a moisture-free environment is because it will absorb moisture from the air, which will evaporate into steam when you print with it, reducing print quality.
What is the basic principle of 3D printing?
Every 3D printer builds parts based on the same main principle: a digital model is turned into a physical three-dimensional object by adding material a layer at a time. This where the alternative term Additive Manufacturing comes from. 3D printing is a fundamentally different way of producing parts compared to traditional subtractive (CNC machining) or formative (Injection molding) manufacturing technologies. In 3D printing, no special tools are required (for example, a cutting tool with certain geometry or a mold). Instead, the part is manufactured directly onto the built platform layer-by-layer, which leads to a unique set of benefits and limitations. The process always begins with a digital 3D model – the blueprint of the physical object. This model is sliced by the printer’s software into thin, 2-dimensional layers and then turned into a set of instructions in machine language (G-code) for the printer to execute. From here, the way a 3D printer works varies by the process. For example, desktop FDM printers melt plastic filaments and lay them down onto the print platform through a nozzle (like a high-precision, computer-controlled glue gun). Large industrial SLS machines use a laser to melt (or sinter) thin layers of metal or plastic powders.
Why are companies exploring 3D printers beyond prototyping?
3D printing’s agile ability to turn digital models into solid objects continues to attract attention and now has many manufacturing companies adding the technology to their production processes, even if they outsource the printing capability itself. Fortune 500 companies, such as General Electric, Boeing, and Ford, have made headlines for incorporating 3D printing into their in-house parts manufacturing processes. But beyond the headlines, many other companies recognize the potential of 3D printing and are closely researching how and when they should invest in the technology.
Why is 3D printing a good choice?
3D printing, also known as additive manufacturing (AM), could be a game-changer for manufacturing, enabling significant savings of cost, time, and materials. In traditional manufacturing, parts are made in large quantities at centralized factories, then shipped to consumers. 3D printing can manufacture parts within hours, which speeds up the prototyping process. This allows for each stage to complete faster. When compared to machining prototypes, 3D printing is inexpensive and quicker at creating parts as the part can be finished in hours, allowing for each design modification to be completed at a much more efficient rate.
What are the three uses of 3D printers?
- Print Organs: 3D printing has been used to print organs from a patient’s own cells. This means that patients may no longer have to wait a long time for donors in the future. In the past, hospitals implanted structures into patients made by hands. 3D printing has drastically improved this process.
- Print automotive parts: Ford Motor Company uses 3D printing to make prototypes of many parts in their vehicles, such as cylinder heads, brake rotors, shift knobs, and vents. 3D printing was used at Ford’s Torrence Avenue Assembly Plant for the production of the Explorer and EcoBoost engines.
- Print aerospace parts: Recently, NASA’s rocket engine injector made from a 3D printer passed a major hot fire test. In the test, the rocket engine injector generated ten times more thrust than any injector made from 3D printing in the past.
How do you make a 3D printer aerospace part?
Due to the typically short runs of aircraft parts, the aerospace industry uses additive manufacturing for a great deal of its production. The technology can produce intricate parts that are more resilient and lightweight compared to those made using traditional techniques, which is an obvious bonus. Aerospace parts that can be created using 3D printers often include internal channels for conformal cooling, internal features, thin walls, and complex curved surfaces. 3D printing processes can create highly complex and lightweight structures with high stability whilst allowing for the consolidation of multiple parts into a single component.
What is FDM used for?
FDM printing is a commonly used additive manufacturing processes for fabricating prototypes and functional parts with common engineering plastics. These machines are used to design 3D models and patterns used in the research and development phase of numerous products in multiple industries. FDM printers have built a sustainable reputation in the automotive, medicine, engineering, electronic, and education industry.
What is an example of additive manufacturing?
Additive manufacturing is all about building an object, pattern, or model layer by layer. The beauty of its design revolves around its simple yet detailed process. For example, instead of milling a workpiece from a solid block, additive manufacturing builds the part up layer by layer from material supplied as a fine powder. Various metals, plastics, and composite materials can be used. Additive manufacturing is relevant in many areas and for numerous industries.
What are the benefits of additive manufacturing?
Additive manufacturing simplifies the printing process to an extent where even the average joey can enjoy an out of the box printing experience. Additive manufacturing aids users in printing assemblies as a single piece. That’s you get to save money from every printing process. Additive manufacturing also gives users the opportunity of printing multiple movable parts as a single piece. Compared to other conventional manufacturing processes, additive manufacturing helps you enjoy a simplified yet highly accurate printing process.
How can 3D printing be used in manufacturing?
The manufacturing industry is always looking at new and innovative ways of working, and in recent years, 3D printing has been at the forefront. Advancements in 3D printing technology, equipment, and materials have resulted in the costs being driven down, making it a more feasible option for general manufacturing use.
- Low volume manufacturing
- High volume manufacturing
What does FDM mean?
FDM means Fused deposition modeling. FDM is regarded as a 3D printing technology often used to print 3D models and patterns. FDM machines can be found in almost every industry. The 3D printers are renowned for their ability to create 3D models of high quality with high accuracy and durability at cost-efficient rates.
How durable are 3D printed items?
It can depend on what material you use, but even cheap abs and PLAis extremely durable. For seriously strong stuff, you can use PETG, Polyflex, Polymax, and flexible materials. But yes – parts are as good as commercially produced parts, in many cases stronger and lighter. To a large extent, for FDM machines, it depends on the orientation you print them in. So the same part can be printed in different orientations, and one will be weak and break easily, and the other will be strong, flexible, and hard to break. Getting really good 3d printed parts is as much an art as a science.